15 Asset Management Best Practices for Better Efficiency and Reliability
Downtime can cost thousands (if not millions) of dollars in the industrial and manufacturing sectors.
Effective asset management is key to reducing that downtime, as well as staying productive, efficient, and competitive.
Regardless of the product you’re shipping or service you’re offering, ensuring that your assets are optimized, reliable, and safe is essential.
From SOPs and predictive maintenance to leveraging cutting-edge technologies like IoT and digital twins, we’ve identified some of the best practices to elevate your asset management strategy.
1. Implement an Asset Management System (AMS)
At the core of efficient asset management is having the right tools in place. A robust AMS or a Computerized Maintenance Management System (CMMS) helps companies track assets in real-time, offering visibility into their condition, location, maintenance schedules, and operational performance.
This kind of system acts as a single source of truth, reducing errors, minimizing downtime, and streamlining maintenance tasks. An AMS or CMMS is a must for asset management.
(Hint: Leverage a VMMS - Visual Maintenance Management System - for even smoother operations and better clarity.)
2. Standardize Procedures & Documentation
A key element of good asset management is having standardized procedures in place. Developing and adhering to consistent Standard Operating Procedures (SOPs) for asset maintenance, repair, and operations minimizes the risk of human error (Ralph talks about this).
Make sure that all asset-related documentation—manuals, instructions, and maintenance histories—are easily accessible and up-to-date.
Visual SOPs can be a game-changer for your organization and operations. And digitized 3D SOPs can support your technicians even more.
3. Manage Asset Lifecycles & Plan Replacements
Assets have lifespans, and knowing when to upgrade or replace them is critical to preventing downtime. Planning downtime for repairs and replacements is more efficient than halting production without notice.
Lifecycle management involves tracking the performance and cost of assets over time, calculating the total cost of ownership (TCO), and making informed decisions on whether to maintain, upgrade, or replace them.
Organizations that know how to manage asset lifecycles are able to maximize ROI and ensure that their operations continue smoothly without unexpected disruptions.
4. Centralize Documentation & Asset History
Keeping all asset-related documents—such as maintenance logs, inspection reports, and upgrade histories—in a centralized repository simplifies management and ensures that everything is easily accessible. Excellent documentation saves time and reduces confusion, ensuring that decisions are based on accurate, comprehensive data.
However, centralizing documentation becomes significantly more useful when it’s digitized. Using software that can hold your asset history, standardize your procedures, and computerize your maintenance management can be critical in staying efficient and reliable. (We have a solution that actually lets you do all of this and see your assets in 8k, visual context.)
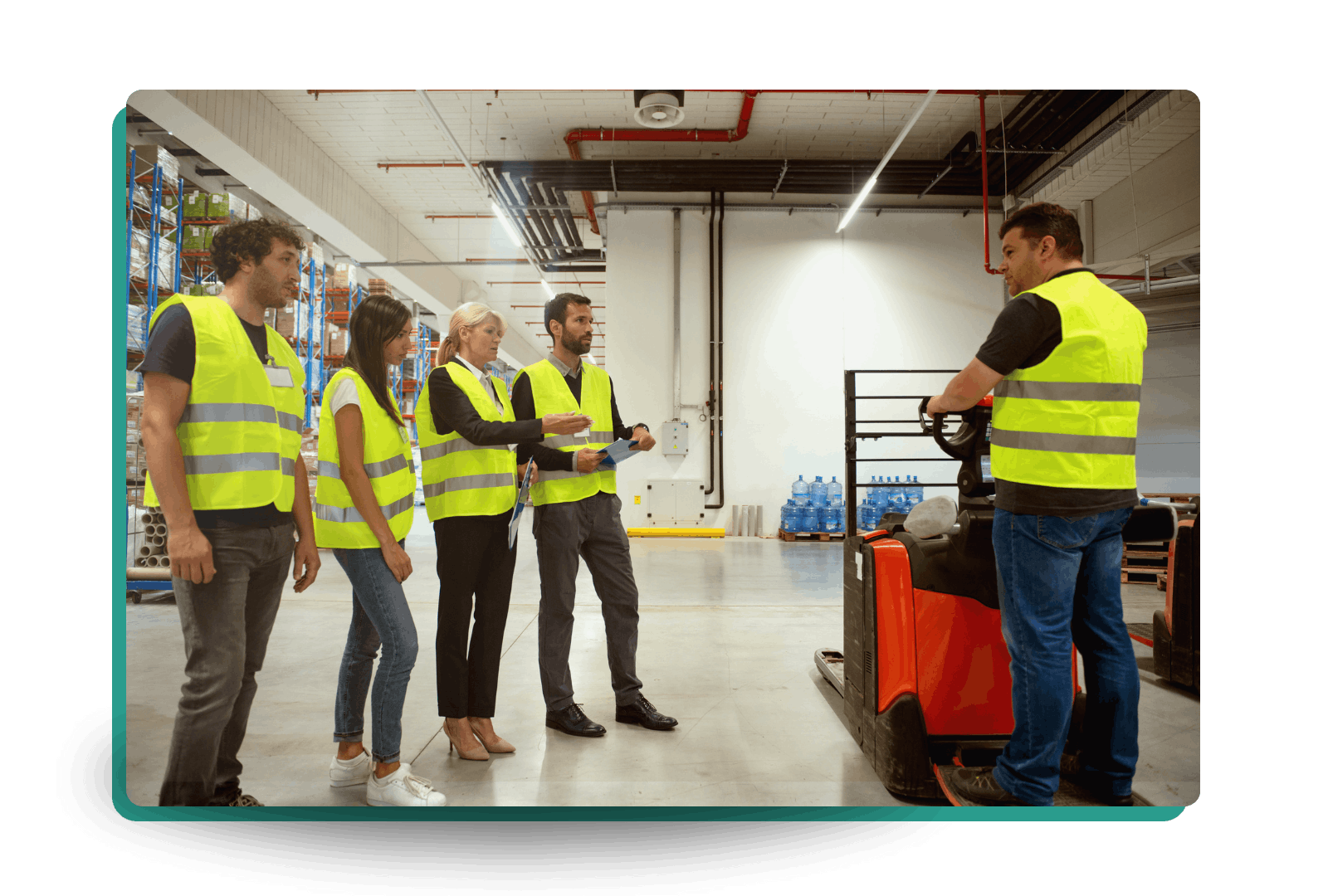
5. Optimize Spare Parts Inventory
Nothing is worse than having a machine go down only to realize you don’t have the necessary spare parts on hand. We mentioned unplanned downtime: this is essentially one of the worst case scenarios as it exacerbates the problem and extends time offline.
Optimizing your spare parts inventory is essential for reducing downtime during asset failures. Maintaining an optimal level of critical spare parts ensures that repairs can be done quickly without overstocking and tying up capital in unused inventory. There’s definitely a balance, and the best managers know how to navigate spare parts inventory.
6. Capture Knowledge & Train Your Workforce
Capturing and delivering best practices could be much higher on this list. Best practices executed consistently across a workflow is invaluable for efficient and reliable asset management.
Effective knowledge capture involves documenting and storing critical procedures, best practices, and asset-specific details, while providing supporting visuals and examples. This, along with robust training programs, ensures that newer employees can quickly come up to speed, reducing operational risk and improving long-term performance.
Unfortunately, expertise often retires along with senior employees, causing institutional knowledge to literally walk out the door. Don’t let this happen to your team: leverage an immersive training environment that captures and delivers your facility expertise.
7. Ensure Regulatory Compliance
Regulatory compliance is a central concern in asset-heavy industries. Failing to meet environmental, safety, or operational regulations can result in fines, shutdowns, or worse.
By using an asset management system to track compliance requirements—such as ISO 55000 or local safety standards—you can stay on top of inspections, certifications, and audits, ensuring smooth and uninterrupted operations.
8. Foster Cross-functional Collaboration
Asset management doesn’t solely fall under the responsibility of the maintenance department. It requires a cross-functional approach, with operations, finance, and other teams all working together to optimize the use of assets.
Clear communication, consistent workflows, and intentional collaboration between departments help ensure that asset priorities align with broader business goals.
9. Track Key Performance Indicators (KPIs)
To truly understand how well your assets are performing, you need to track Key Performance Indicators (KPIs). Common KPIs in asset management include:
- Mean Time Between Failures (MTBF) – How long an asset runs before failing.
- Mean Time to Repair (MTTR) – How long it takes to repair a failed asset.
- Overall Equipment Effectiveness (OEE) – A comprehensive measure of how well an asset performs against its potential.
Regularly monitoring and analyzing these KPIs can highlight inefficiencies and provide actionable insights for continuous improvement. Read more about these KPIs here (an informative blog by Brightly)
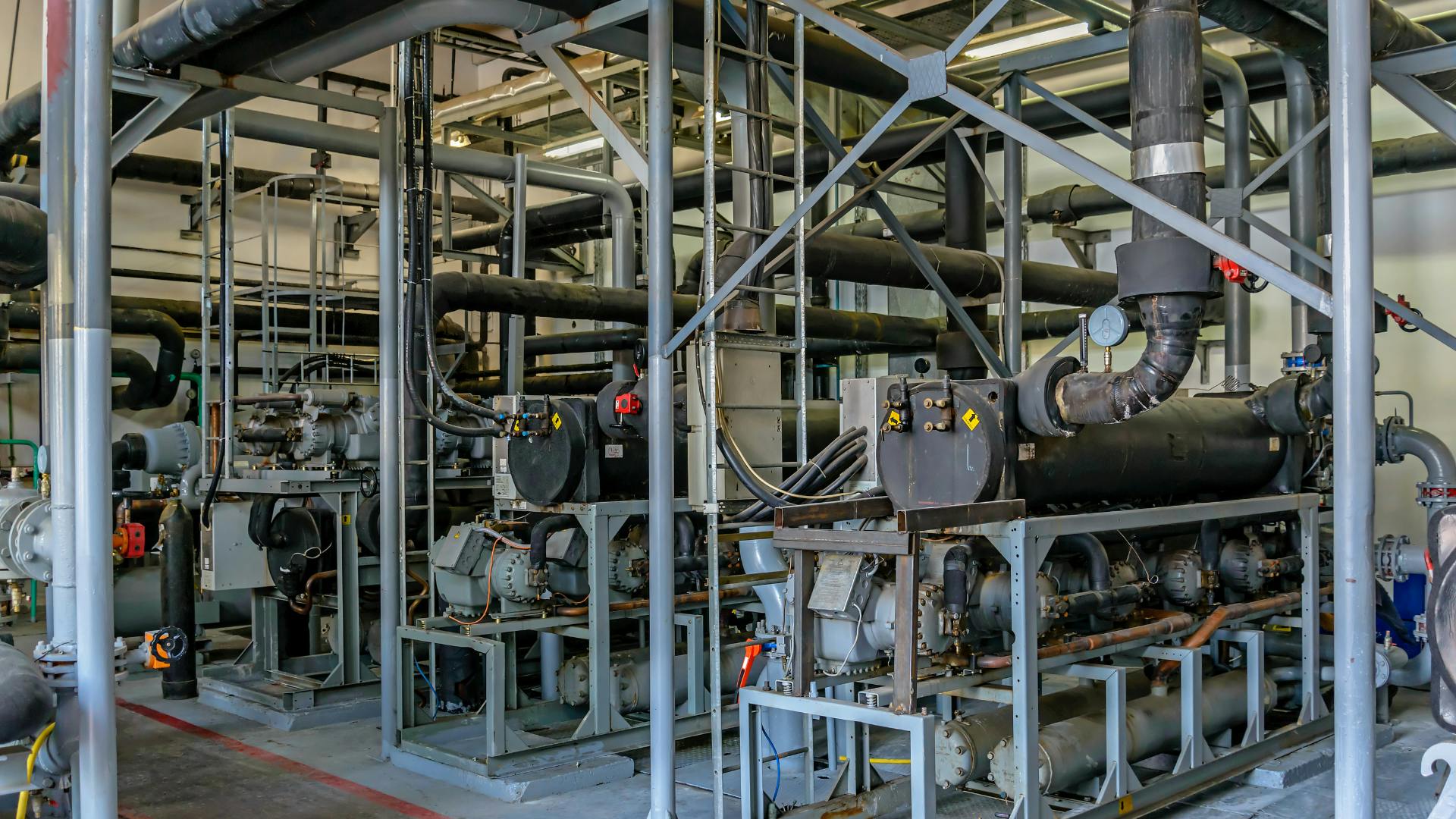
10. Prioritize Energy Management & Sustainability
Many industrial assets consume significant amounts of energy, which directly impacts operational costs and environmental sustainability. What if you could maximize production and minimize waste by implementing energy management practices? It’s possible.
We would suggest starting with tracking energy usage, identifying inefficiencies, and upgrading to more energy-efficient equipment. These steps can lower costs and align with sustainability initiatives, and there are many tools available to help with this type of initiative.
11. Leverage Data Analytics for Better Decision Making
We live in a data-driven world. (No, ChatGPT did not write that sentence.)
Unsurprisingly, analytics play a significant role in modern asset management.
Teams that collect and analyze data from assets can identify inefficiencies, predict failures, and optimize performance. Relevant data can be used to make informed decisions about repairs, replacements, and process improvements, ultimately reducing costs and enhancing productivity.
Teams that can use data analytics to their advantage will be able to experience better efficiency and reliability in their asset management.
12. Plan for Resilience & Risk Management
A solid asset management strategy incorporates risk management. And with risk management, a reactive posture is costly and unpredictable, whereas a proactive stance is strategic and anticipatory.
Identifying critical assets, planning for potential failures, and creating contingency plans help organizations stay resilient in the face of disruptions. Having disaster recovery strategies, spare capacity, and emergency protocols in place ensures that operations can continue smoothly, even in worst-case scenarios.
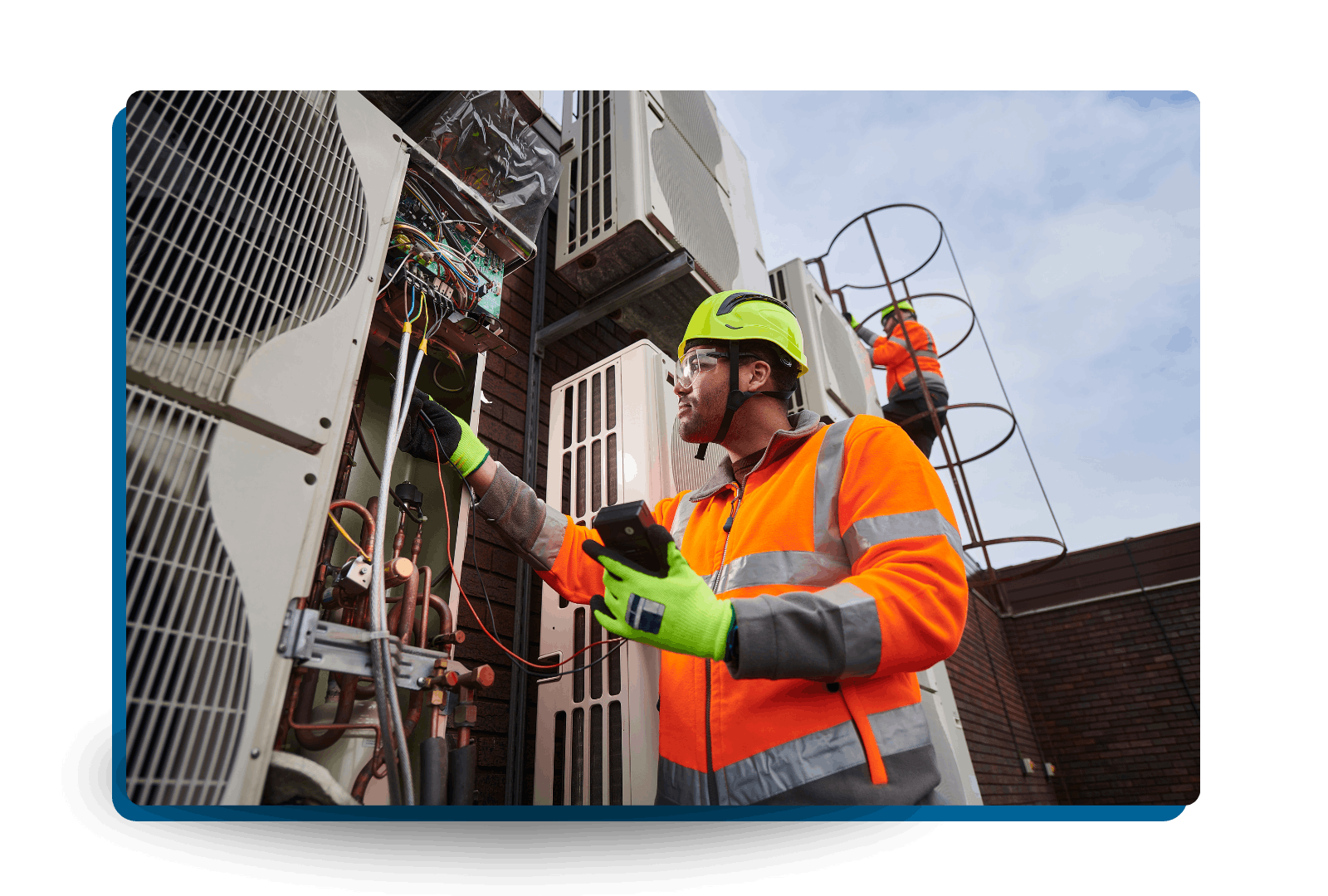
13. Harness the Power of Digital Twins for Asset Visualization
Imagine having a 3D model of your physical assets that you can view and interact with remotely. Digital twins are just that: virtual replicas of physical equipment and infrastructure that allow real-time monitoring and management.
With digital twins, you can visualize a space objectively, optimize operations, streamline troubleshooting, revolutionize your training, digitally store your SOPs, and make data-driven decisions on repairs, upgrades, or replacements.
Your asset management, process management, and training initiatives can be revolutionized with a 3D digital twin (we’ve seen it happen).
14. Move Toward Predictive & Preventive Maintenance
We all know the worst type of maintenance is performed after assets have already failed.
Preventive maintenance (PM) ensures that regular inspections and servicing happen at set intervals based on time or usage. These practices are proactive and save significant money by preventing equipment from breaking down unexpectedly.
Additionally, modern asset management leans heavily on predictive maintenance (PdM), where wireless sensors, IoT, and advanced analytics predict potential failures before they occur. By tracking data on factors like vibration, temperature, and wear, you can forecast when equipment will need maintenance, extending its lifespan and preventing costly downtime.
15. Integrate IoT & Automation
Speaking of IoT (Internet of Things), there has been a recent increase in its usability within asset management. Wireless sensors have revolutionized the way we monitor and maintain equipment. IoT sensors provide real-time data on asset health, such as temperature, vibration, and usage.
Automation allows for instant alerts when thresholds are crossed, ensuring that maintenance work orders are triggered automatically. With real-time data and informative algorithms, organizations can minimize the need for manual intervention, reduce response time, and enhance overall efficiency.
And regardless of any given stance on Industry 4.0 buzzwords or the tech it speaks to, it’s not a stretch to see where the future of facility and asset management is headed!
Start With One
Downtime is expensive. Effective asset management is a powerful way to yield efficiency and reliability without compromising on production.
If your team hasn’t already, begin the process of adopting these 15 best practices. Our suggestion is to start with one.
Which seems easiest to implement right now? Which strategies would you like to learn more about?
And once you’ve started this process, your asset management will see a continuous trend towards better efficiency and reliability.
If you’re interested in learning more about effective Asset Management by leveraging the power of a VMMS, reach out to our team at Aetos Imaging and let us partner with you on your digital transformation journey.