Just Buzzwords or Actual Breakthroughs? Defining 3 New-Era Terms in the Current Industrial Movement.
We live in a digitized world.
The overwhelming majority of people have fully embraced the trend toward digitization. All it requires is a smartphone, laptop, or tablet - one of which is being used right now to read this sentence.
By using our phones for a large percentage of our daily activities, society is fully integrated with the digital movement, and likely can’t imagine going a day without. With our mobile devices, we access recipes, bank accounts, memories, passwords, music, podcasts, sports scores, emails, socials, and much more on a minute-by-minute basis.
In the digital world, the more intentionally connected you are, the more streamlined your personal operations become.
The same is true when digitizing an industrial/manufacturing space: the more intentionally connected they become, the more streamlined their operations will be.
Transitioning to a digital lifestyle was a gradual inevitability for all of us; as we interacted with intuitive interfaces, our adoption of digital resources became more prevalent and beneficial.
Similarly, the traditional methods of facility management in the industrial world are gradually progressing. The adoption of an intentionally digitized space is yielding better operations - ranging from safety to training to work order management to improved production and beyond.
The organizations that embrace the “digital industrial revolution” will survive and thrive in the era to come.
The others who fail to make the transition? Name an industrial plant that refuses to use assembly line concepts: they don’t exist.
During this “digital industrial revolution” there have been a lot of new terms emerge. Some are confusing, some are redundant, and some just simply exist to sell a product.
Three key terms often used in discussions about this technological revolution are IIoT (Industrial Internet of Things), Digital Transformation, and Industry 4.0.
Each of these vocab words have their own lane, and each are critical in shaping the modern industrial landscape. Understanding their differences and “interconnectedness” is crucial for any organization looking to stay ahead - or at least stay competitive - in the digital age.
IIoT: The Industrial Application of IoT
Let's start with the Industrial Internet of Things (IIoT).
Imagine a factory where machines communicate with each other, where a conveyor belt alerts the maintenance team about a potential breakdown before it happens, or where production data is instantly analyzed to optimize processes. This is IIoT in action.
According to TechTarget.com, IIoT “is the use of smart sensors, actuators and other devices, such as radio frequency identification tags, to enhance manufacturing and industrial processes.” Simply put: IIoT is a unified way to send and receive information to and from every asset for more efficient operations.
Like how we’ve adopted our cell phones to be our primary source of personal information and communication, IIoT is about connecting industrial equipment and devices to the internet and each other, enabling them to collect, exchange, and analyze data in real-time.
This connectivity leads to increased automation, improved efficiency, and reduced operational costs. IIoT is a crucial component in modern industries, allowing for smarter manufacturing and enhanced decision-making processes.
Digital Transformation: Beyond Just Technology
Digital Transformation is a broader, more holistic concept.
The name is the definition itself: adopting new technologies and fundamentally rethinking how an organization operates and delivers value in the digital era.
In order to move forward in the digital transformation, management teams are being asked to take their operations to a new level of connectivity and clarity. This process can be challenging at first, but can offer incredible return on investment.
The digital transformation process involves integrating digital technology into every aspect of a business, leading to profound changes in how businesses function and interact with their internal and external stakeholders. In a February 1 article by chicagobusiness.com, “The manufacturing sector has undergone a profound transformation, driven by new advancements in technology that have reshaped its future.”
The article goes on to express that organizations must “adapt or become obsolete” in the industrial and manufacturing industries; although this change is challenging - and perhaps divisive - its significance is directly tied to future progress.
To take it a step further, it’s also about cultural change, encouraging organizations to embrace innovation, adaptability, and continuous learning. From cloud computing to AI, and including IIoT, digital transformation is reshaping the corporate world, making businesses and their processes more agile, customer-centric, and competitive.
Industry 4.0: The Fourth Industrial Revolution
Last: Industry 4.0. Often referred to as the “fourth industrial revolution”, this term takes us into the realms of smart factories and cyber-physical systems.
Industry 4.0 represents the convergence of advanced manufacturing techniques with IIoT, leading to the creation of smart, interconnected industrial ecosystems. Here, physical and digital technologies merge, creating highly automated, self-monitoring systems that can predict failures, adapt to changes, and communicate with other systems and with humans.
Industry 4.0 encompasses IIoT as one of its components but goes beyond by integrating various technologies like AI, cloud computing, and big data analytics to revolutionize manufacturing and industrial processes.
Just as each previous industrial revolution dynamically altered the status quo, so too will Industry 4.0 within the manufacturing space. And just as companies needed to change to survive, the same will prove true in this iteration as well.
A leader in the conversation - 4.0 Solutions - identifies the concept of a Unified Namespace (UNS) as an Industry 4.0 solution: delivering a “common ground where all data is standardized and shared, ensuring seamless communication across different systems.”
In other words: Connection across systems grants better communication, understanding, processes, and visibility - leading to optimized performance and faster resolution.
Those in the industry know: Industry 4.0 is a legitimate transition in manufacturing and will indicate which organizations adopt, survive, and thrive, and which ones will write their proverbial tombstones next to the companies that didn’t embrace the assembly line.
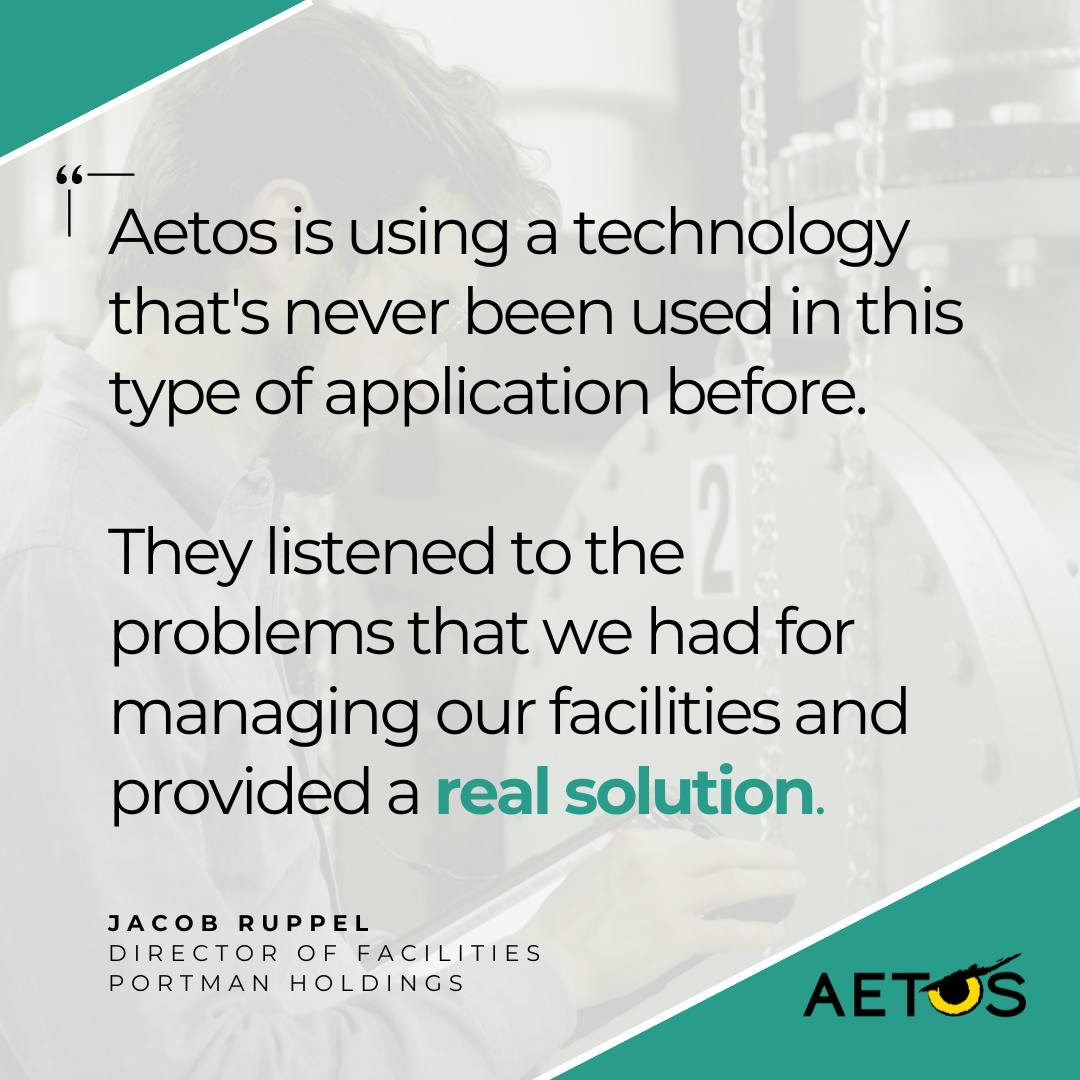
Visualize the Digitization Process
In envisioning the future of industrial technology, Aetos grasped the exciting potential of combining 3D scanning, visual asset management, and IoT integrations. This unique blend creates a dynamic digital space where physical environments are meticulously mapped and managed with unparalleled precision.
Imagine walking through a factory where every machine - every component - is not just a physical entity but also a detailed digital asset, managed and detailed on a single visual platform. Aetos offers an exact, interactive replica of physical assets, allowing for remote inspection, planning, and problem-solving.
This digital replication extends into visual management, where these 3D models are not standalone assets but parts of a larger, interconnected system. Our platform integrates real-time data provided by IoT devices, offering a comprehensive view of each asset's performance, health, and maintenance needs.
In such an environment, decision-makers can virtually navigate through their operations, interact with equipment, update and sync their systems, and make informed decisions based on real-time data. The synergy between visual asset management and IIoT integrations revolutionizes maintenance, monitoring, and company-wide operational functions.
We’re transforming physical spaces into a fully integrated, interactive, and intelligent digital ecosystem. Aetos is intentionally partnering with plant managers and upper management alike to help their facilities on the digital journey.
This fusion represents a significant leap in operational efficiency, predictive maintenance, and overall asset management, marking a pivotal point in the journey towards truly smart industries. Those that fail to adopt IIoT, Digital Transformation, and Industry 4.0 concepts will fail to function in the future.
Let Aetos Be Your Partner in Your Digital Journey
As businesses continue to navigate the complexities of the digital world, understanding and implementing these concepts is essential for staying competitive and future-proof.
Let Aetos be your partner, assisting you and your facilities to take the next steps. By embracing IIoT, Digital Transformation, and Industry 4.0, businesses can unlock new levels of efficiency, innovation, and growth, propelling them into a successful, digitally-driven future.
Although digitizing a non-digital space could seem insurmountable, we assure you it’s very possible and attainable.
Aetos is here to help organizations like yours digitize (and visualize) your operations. Take the next leap in the digital transformation. The screen you’re reading on is proof you’ve done it before.