These Phrases Are Symptoms of Ineffective Process Management
Heard any of these before?
“That’s not how we do it at the other plant.”
“Why didn’t anyone tell us this was happening?”
“We’re constantly playing catch-up with safety checks.”
These phrases pop up whenever workers are misaligned and are almost always the symptoms of ineffective process management.
They signal deeper issues. The symptoms of poor process management can silently erode efficiency and safety. In fact, according to IDC research, inefficient processes cost organizations up to 20-30% of their annual revenue.
Weak process management yields weak communication, methods, and eventually weak production.
Strong process management yields strong communication, methods and eventually strong production.
Essentially, process management actually gauges how an organization performs.
And unfortunately in the industrial environment, process management often takes a back seat to more visible operational challenges like output, staffing, safety, and inventory control.
The hidden inefficiencies and disorganization that stem from poor process management can have significant consequences.
Facility managers are always looking for streamlined strategies to get a firmer grip on their facility. If processes aren't assessed and improved, FMs may continue to hear the following symptomatic phrases and struggle with deeper operational issues within their organization.
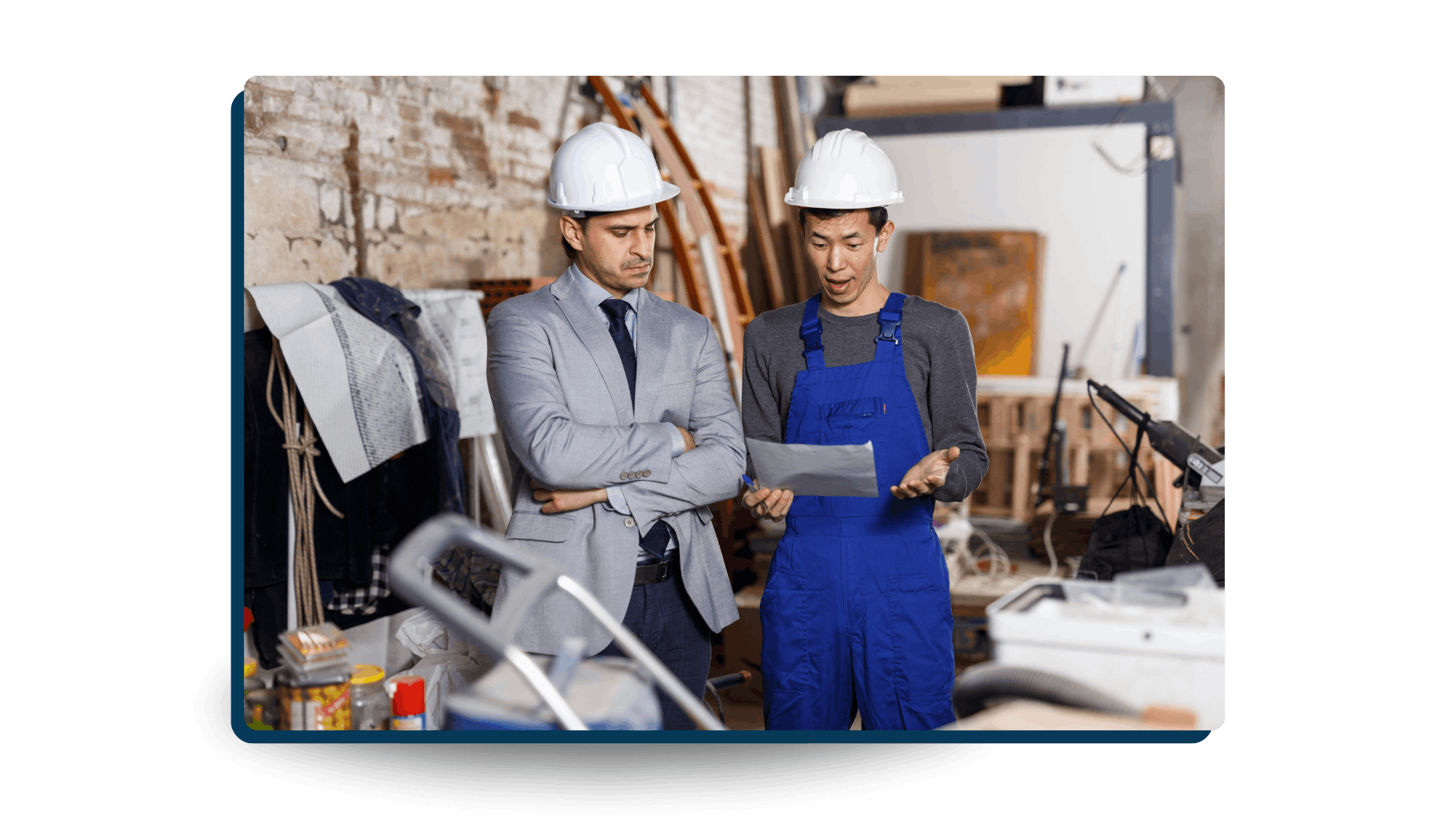
Phrase: “Well how do you do it?”
Symptom: A Lack of Standardization Across Sites
Inconsistent processes between different locations or even departments within the same facility can create confusion and inefficiency.
When each site or team follows its own version of standard operating procedures (SOPs), it becomes nearly impossible to maintain uniform quality, productivity, and safety standards across the board.
Phrase: “That’s not what I was told!”
Symptom: Siloed Communication Between Teams
Similar to differing versions of SOPs, many industrial operations are plagued by poor communication between departments like operations, maintenance, and safety teams.
This lack of cross-functional communication can result in critical information being missed, duplicated efforts, or misaligned priorities—all of which lead to avoidable delays and issues in the production process.
Phrase: “Just sign at the bottom. They never check anyways.”
Symptom: Poor Compliance and Safety Processes
Safety is paramount in complex facilities. And process management is essential for ensuring compliance with safety and environmental regulations. However, many facilities lack the tools to consistently enforce compliance across all processes.
Without clear visibility into how safety protocols are being followed—or the ability to quickly address non-compliance—facilities risk fines, operational shutdowns, and even endangering workers.
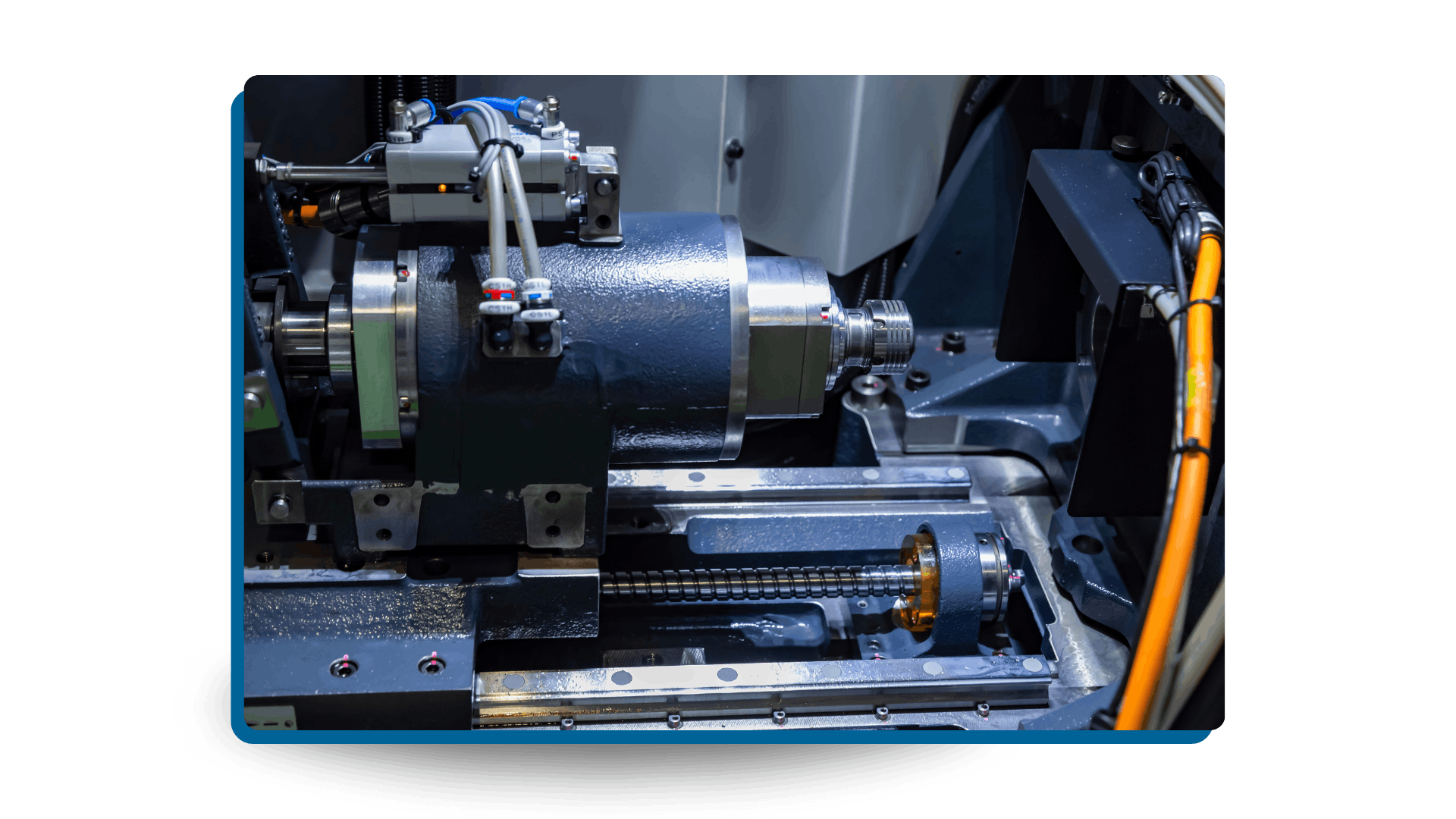
Phrase: “Call Joe. He’s the one who knows how to do this.”
Symptom: A Lack of Transfer of Institutional Knowledge
Organizations are hamstrung when best practices are undocumented and instead live in the heads of the senior operator. And worse, when Joe retires, years of accumulated knowledge goes with him.
The industrial sector faces a significant challenge: without adequate systems in place to capture and retain operational knowledge, younger or less experienced workers struggle to maintain established processes, leading to a decline in productivity and safety.
Phrase: “This is the way we’ve always done it.”
Symptom: Outdated or Inflexible Processes
Many industrial facilities are stuck using outdated processes that were developed years ago and have not been adapted to modern needs.
These legacy processes are often inflexible, making it difficult to adjust when production demands change or when new technologies could improve efficiency. As a result, facilities may find themselves locked into workflows that no longer serve their best interests, creating bottlenecks and inefficiencies.
Phrase: “I know we have the data, but it’s all over the place.”
Symptom: Disconnected Data Systems
In many industrial facilities, process management suffers because critical data is scattered across multiple systems. (Maintenance data might reside in one system, while production data lives in another, and neither integrates with operational oversight.)
This lack of data integrity and accessibility leads to misalignment where decision-makers can’t access a complete, real-time view of operations. The effect? Delays in identifying issues and missed opportunities for optimization.
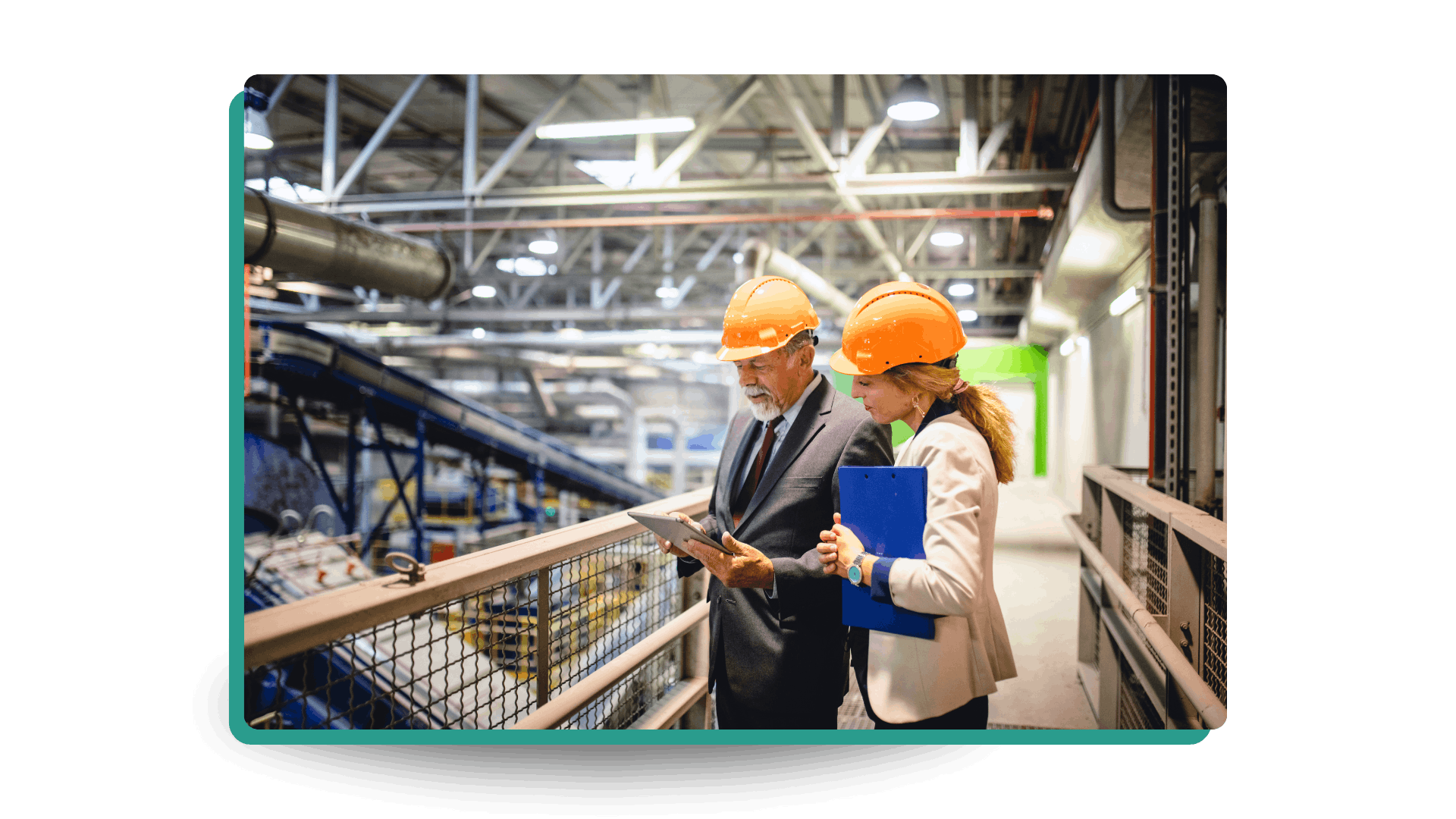
Phrase: “Yeah, but I don’t know if this process is actually working.”
Symptom: Limited Visibility & Understanding of Processes
One of the most frustrating aspects of managing industrial facilities is the difficulty in understanding how well processes are actually working.
With limited visibility into the performance of processes, organizations often rely on guesswork to identify inefficiencies, leading to reactive rather than proactive management of operations.
Phrase: “We Need Something Different.”
Symptom: It’s time to assess and act.
Although the aforementioned issues may not always be visible, the consequences are real: lost time, wasted resources, and increased operational risks.
Have you experienced any of the listed problems? Or heard any of the comments within your four walls? Could it be time to elevate process management within your organization?
Improved processes can actually alleviate, mitigate, and sometimes even eliminate the “more visible” operational challenges.
With stronger processes, you can start to enable stronger production – and start to hear things like “It’s so nice to all be on the same page!”
Don’t wait for the symptoms to escalate into full-blown operational inefficiencies. Conduct a process audit, engage your team, and assess where improvements are needed. Strengthening your process management today will lay the foundation for tomorrow's success.