Manufacturing Training: Revolutionary 3D Visual Courses
Manufacturing training has been revolutionized with immersive 3D visual courses from Aetos Imaging, tailored to improve the training process for industrial and manufacturing environments.
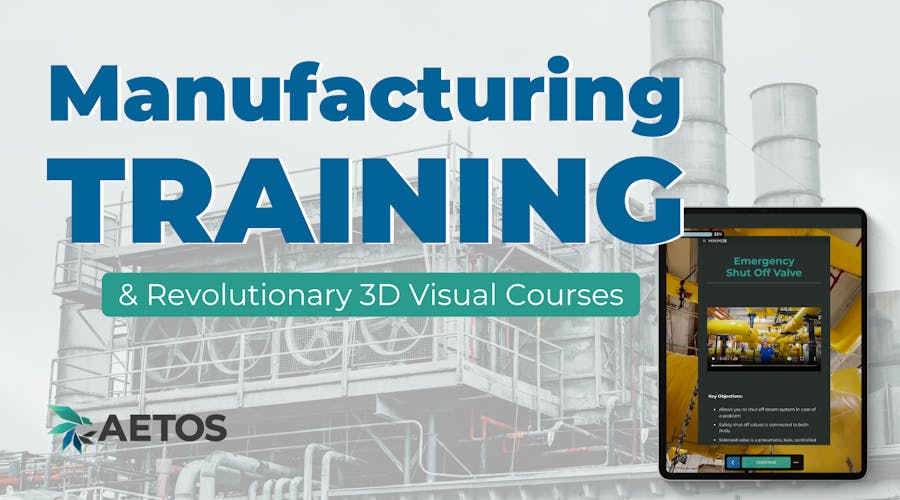
What is a 3D Visual Manufacturing Training Course?
Traditional training methods are evolving, and the need for innovative solutions has never been greater. There aren't many LMS for manufacturing or the industrial space in general, and Aetos is here to fill some of those gaps.
This pivotal shift is driven by advancements in technology, specifically the rise of 3D visual training courses in the industrial and manufacturing spaces.
3D visual courses revolutionize how skills and safety protocols are imparted, making training more engaging and effective. In fact, according to this study on visual learning, "Visual content boosts recall to about 65%, compared to only 10–20% from spoken or written material."
Aetos is intent on integrating these visual methods to enhance workplace training, foster increased understanding, better safety, improved quality of life, and retention among employees.
In the energy, utilities, and manufacturing industries, training is essential for bridging the skills gap and ensuring consistent training across the workforce.
This article aims to explain components of creating an effective 3D visual learning experience, examine the significant benefits these courses offer, and outline how prioritizing safety and clear communication can elevate training in the industrial sector.
Aetos is taking an immersive approach - similar to Google Street View combined with YouTube and an LMS. Your real built environment as the interface. Videos, quizzes, step-by-step visualized training modules, and more, all inside. You can sign up to experience it for yourself from our homepage here!
This visual experience allows trainees to navigate the manufacturing environment virtually, aligning with modern learning styles and enhancing training delivery methods. We built this learning system specifically to support your boots-on-the-ground employees like your operators and technicians, and are excited to dive deeper into the how/why.
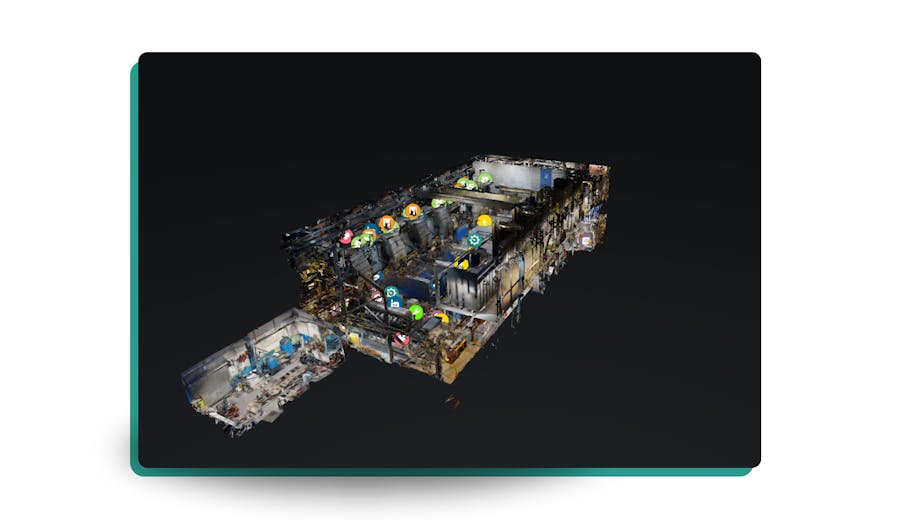
Enhanced training comprehension for facilities workers
Using 3D environments for learning opportunities enables companies to convey complex concepts more effectively.
Employees can experience realistic work settings, which assist in understanding company policies and safety procedures. By leveraging this technology, industrial & manufacturing companies can enhance both technical skills and soft skills, contributing to a well-rounded manufacturing career for employees while improving product quality and adherence to safety standards.
Traditionally, manufacturing training involves classrooms for training sessions or on-the-job learning, focusing on theoretical knowledge and practical skills. However, these methods can be disconnected from the actual manufacturing environment workers operate in, often lacking engaging training content.
Aetos offers a solution by integrating a site-specific 3D visual guide, allowing trainees to experience the facility's actual layout and processes virtually. The value of a 3D visual manufacturing training course lies in its immersive experience, which supports all kinds of training and compliance activities.
It supports effective training by providing a realistic simulation of the production process. This approach can significantly enhance the learning objectives by offering clearer insights into job skills, safety protocols, and company operations.
As a result, this type of learning and training process becomes more effective, interactive, and easily adaptable to the specific needs of manufacturing companies.
The Six Steps to Creating an Effective Visual Training Program
In these six steps, we outline our process of how efficient, yet granular you can make a training program when you have a 3D visual environment as the learning interface for your industrial or manufacturing training environment.
1. Conduct a 3D Scan: First, organizations must establish what spaces they will want their teams to virtually train in. By starting with a site-specific capture with detailed 3D visualization, the facility management team can ensure training materials are accurate and context-specific.
2. Define Training Goals: Establish clear learning objectives that align with the company's training needs and safety standards. When delivering any type of safety procedure, regulatory compliance, or general knowledge transfer, the what of a training is vital when determining the how a team is trained.
3. Develop Training Content: One of the most obvious (yet typically underutilized) steps of the process. Content is critical. Add visual aids such as step-by-step work instructions and interactive scenarios to enhance retention and understanding. You can create content related to any other compliance training platform you already use, or any other type of LMS you already have. Because Aetos provides you with visual context to everything while also including video and photo capabilities, creating new content and adding new training courses has never been easier! In just a few clicks you can create an entire training chapter.
4. Launch Instructor-Led and Online Training: Mix instructor-led sessions using video content with online training quizzes and testing to cater to diverse learning styles and enhance flexibility. Our most efficient customers utilize their in-house subject matter experts for instructor-led training to create short explanatory videos that are housed within the 3D learning environments.
5. Leverage Dynamic Feedback within the Aetos Training Platform: Harness real-time data and training records to transform static modules into immersive, learner-centric experiences. By integrating advanced guidance features directly into the 3D environment, you deliver context-specific support, accelerate skill mastery, and amplify operational safety. This data is also helpful for compliance and training audits - your auditing process will be faster than ever through visual confirmation.
6. Evaluate and Iterate: The goal is to deliver the best possible manufacturing process, as safely as possible. Regularly assess training effectiveness by gathering feedback and consistently updating the training program to address evolving needs and challenges. You can learn more about Aetos processes here.
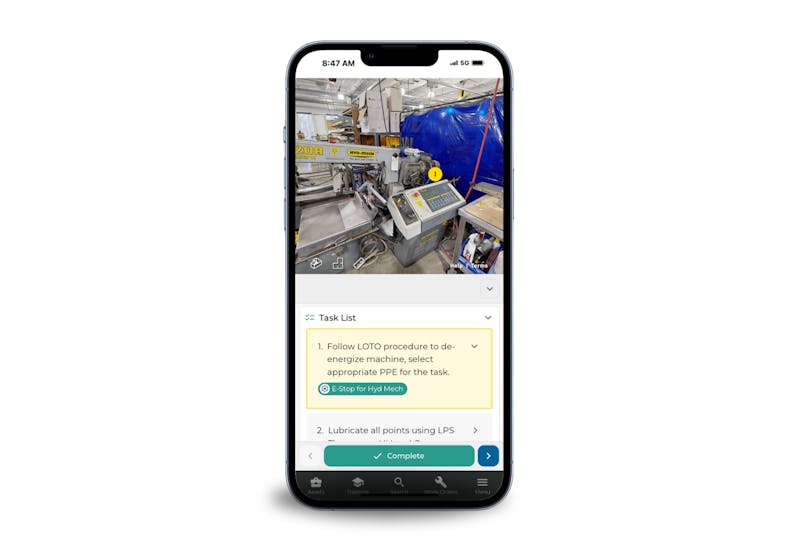
Next-Level Safety Training: A Top Priority for Industrial Companies
3D visual environments elevate safety training by simulating real-world scenarios, allowing employees to practice safety procedures without physical exposure to risks.
These comprehensive training programs reduce the likelihood of accidents by preparing workers for emergencies in a controlled setting, reinforcing their understanding of safety standards and protocols throughout the entire process.
By providing a comprehensive visual overview of the workplace, employees can familiarize themselves with potentially hazardous materials unique to their roles and environments. A proactive approach to workplace safety fosters a culture of awareness and preparedness: an understandably high priority for the manufacturing sector.
With these advanced training methods, manufacturing companies can effectively close skill gaps, communicate safety protocols and improve their response strategies — all while developing skilled employees and meeting business goals.
The result is a safer and more efficient workforce capable of maintaining high product quality and operational standards.
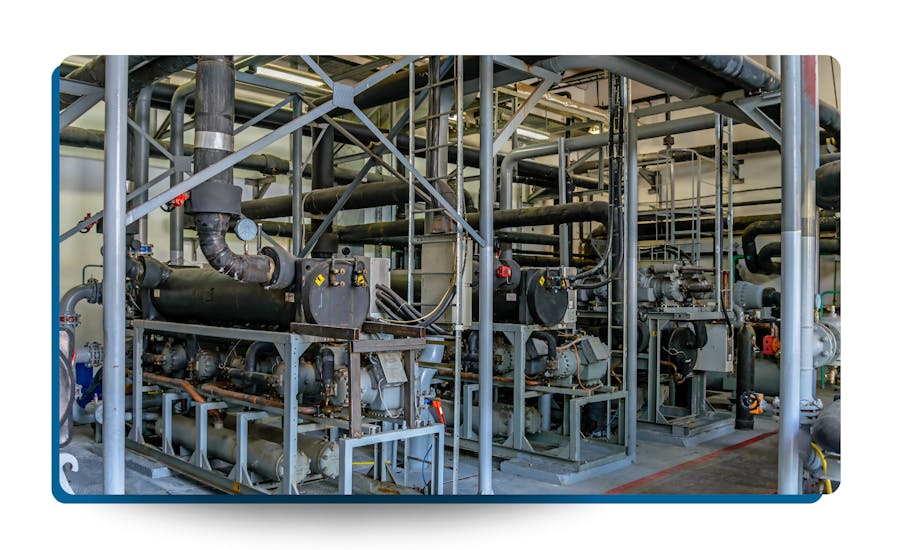
Communicate Work Instructions Clearly in Your Industrial Environment
Traditional manufacturing training systems often rely on generic text documents or instructional videos, which can fail to provide site-specific details. These methods use OEM standard images that might not accurately reflect the particular challenges or configurations of the actual workplace environment.
Aetos changes this dynamic by delivering work instructions in a fully tailored 3D visual environment. With better visual context, employees receive consistent training materials, specific to their facility's layout and equipment.
Such clarity in communication aids in minimizing operational errors and enhances the accuracy and effectiveness of daily tasks.
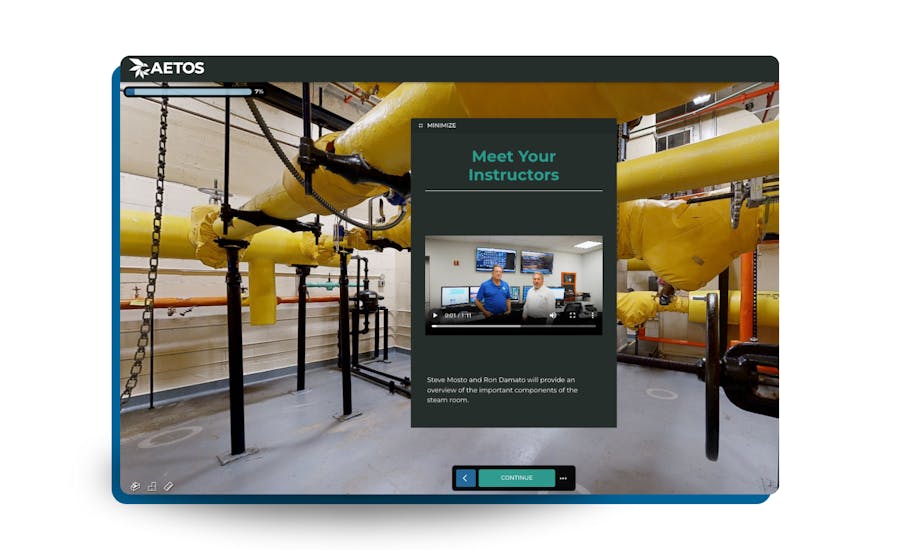
How Aetos has Enhanced Industrial and Manufacturing Production and Operations
Aetos Imaging's 3D visually guided learning courses revolutionize industrial and manufacturing training through relevant videos, interactive quizzing, and site-specific familiarity. You'll find in this research from the eLearning Industry that a visual learning system also supports the majority of workers, "Over 65% of the population is composed of people that learn visually."
This method reduces the need for extensive on-the-job training by creating a site-specific virtual environment that mirrors the actual workspace. Your senior employees can get some of their time back!
Manufacturing employees can practice and reinforce their skills in a controlled setting, diminishing the risk of exposure to workplace hazards.
The overall learning curve is drastically reduced by combining audio, video, and the 3D environment inside of Aetos.
These are some of the primary ways we are altering the way workers can learn across all different types of industrial organizations.
The use of 3D visualization ensures a high level of detail and accuracy, improving safety in dangerous environments by allowing workers to familiarize themselves with their surroundings beforehand. This alignment enhances the training process, making it more engaging and interactive. Workplace safety is heightened, skill gaps are mitigated, and employees are better prepared to tackle practical challenges efficiently.
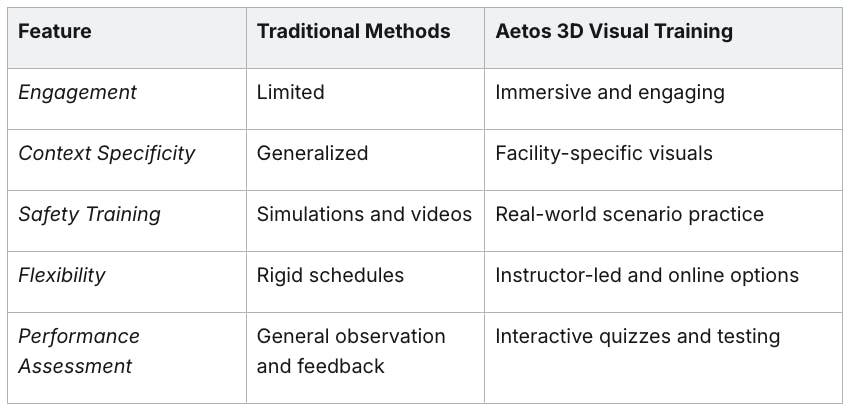
1. Prioritizing safety
Safety is paramount for industrial manufacturing or industrial companies in general, particularly in energy, utilities, and most manufacturing sectors.
Providing a better training delivery method is essential for effective and consistent manufacturing training. With a focus on safety standards and protocols that are essential to prevent workplace accidents, organizations that adhere to proper training goals not only ensures a secure manufacturing environment, but also earns their workers trust.
2. Specialized skill development
3D environments enhance learning by providing immersive experiences, crucial for developing both soft and job-specific skills. This is where we can really have a big impact on process management and quality management with a step-by-step visually guided training inside of our platform.
A visual approach to worker understanding significantly reduces onboarding time and accelerates the acquisition of technical skills. Consequently, most machine operators and maintenance technicians exhibit significantly improved knowledge retention and are better equipped to meet their training objectives.
3. Much-improved on-the-job training
Traditional on-the-job training can be time-consuming and costly due to the need for senior employees to guide new hires through noisy facilities. This can impact production, as those more experienced employees have their biggest impact to your bottom line when they are out on the floor, not in the classroom.
3D training eliminates unnecessary facility tours and minimizes overtime from your most experienced team members. The combination of instructor-led sessions and online training ensures efficient training delivery, saving both time and resources for manufacturing and industrial companies.
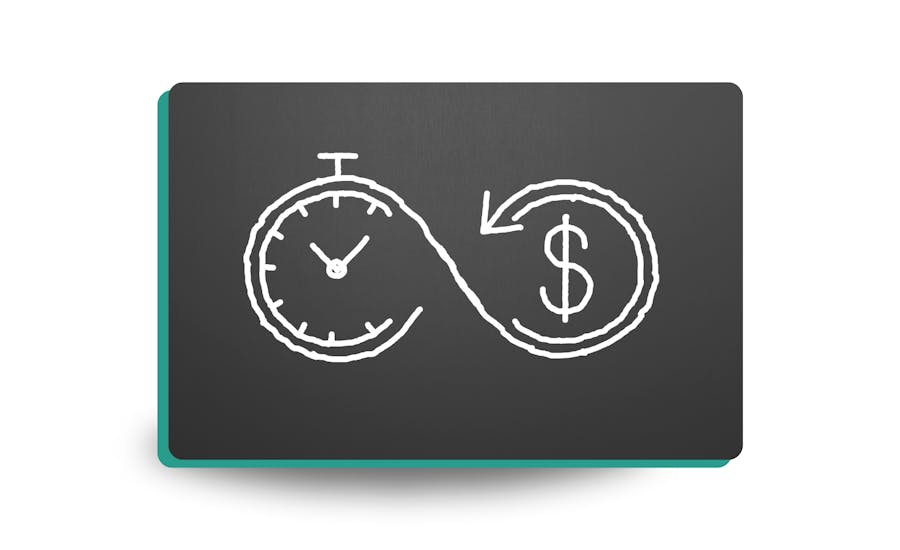
Let Your Workforce Know: Expectations Ahead of Training
Visualized site-specific training courses can provide a strong foundation for new workers. Now, new or incoming operators and technicians can familiarize themselves with their future work environment in a safe, controlled setting. Such preparation ensures they are mentally ready before stepping into the facility.
Make your industrial and manufacturing expectations clear
Using visuals that are an exact copy of the actual equipment and assets workers will handle is crucial. Combining these with quizzes and tests throughout the training solidifies employee understanding of priorities, and how they are to operate or maintain their environment.
It's a proven method that directly aligns training objectives with the workplace, differentiating between learning styles and elevating retention.
Training the managers and supervisors
Managers and supervisors play a key role in employee development. Their leadership reflects the company's commitment to workplace safety and employee growth. By leading training programs with enthusiasm, they underscore the importance of technical skills, soft skills, and safety standards to their team.
Industrial reporting: Learning objectives and training
Incorporating 3D capture into the training process empowers workers and boosts operational efficiency. Because of this, Aetos provides robust tracking of employee progress, supporting individualized learning paths.
With detailed training reports available to leadership, companies can promptly address skills gaps, celebrating achievements and addressing growth areas.

Better manufacturing training is possible. Aetos is intent on enhancing continuous learning in industrial and manufacturing companies, fostering a more productive manufacturing career landscape: best achieved by having site-specific visual context for everything related to your industrial and manufacturing training programs.
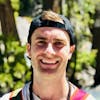
Mitch Graham is a Product Marketing Manager for Aetos Imaging: an Industrial SaaS that is intent on bringing visibility to your industrial training activities, asset management, and other industrial production operations. With a decade of experience in education and technology, Mitch creates content that aims to make sense of everything related to manufacturing training, and learning and development.