What is Continuous Improvement & How Should I Implement It?
To begin, let’s start with the opposite of Continuous Improvement, which can be summed up in a seven word phrase: “Because that’s how we’ve always done it.”
Although this phrase might have legitimacy in some capacities at varying levels and settings, those seven words oppose the principles of Continuous Improvement.
Continuous Improvement is the process – and frankly, the mindset – that seeks better results. It’s in the name: a Continuous Improvement professional, team, or task force is intent on finding ways to push their organization to more productivity and proficiency. It's an ongoing and perpetual process: striving for excellence in the pursuit of efficiency.
This umbrella term includes differing focuses for differing verticals – whether it’s safety, training, production, or maintenance.
Yet the goal remains the same. Continuous Improvement is willing to change the way things are done to yield better (or faster, or safer) results.
Now don’t jump to the wrong conclusions: there’s something to be said about consistency and following a prescribed plan. Continuous Improvement is not disruptive for the sake of disruption, nor is it a magic bullet promising to eliminate all future problems. It's a process that seeks to increase productivity and improve the overall performance of an organization.
When a company has figured out a modus operandi that grants maximum efficiency, there’s power in streamlining consistent operations. Nonetheless, the Continuous Improvement mindset seeks opportunities to correct mistakes, fill gaps, and enhance performance. After all, industries change, technology advances, and pobody’s nerfect.
There are many procedures, programs, philosophies, and even certifications in the realm of Continuous Improvement. Online content (like this helpful blog guide or this comprehensive article) and informative videos are readily available with one intentional search.
The most popular methods that are commonly used for Continuous Improvement initiatives are: PDCA (Plan, Do, Check, Act); LEAN (which focuses on maximizing productivity by minimizing waste); 6 Sigma (a very disciplined, data-driven approach); Kaizen (more of a comprehensive approach to business that is intent on positive change); 5S (Sort, Set in Order, Shine, Standardize, Sustain, + Safety for 6S); and TQM (Total Quality Management).
Essentially, Continuous Improvement can be boiled down to the same procedures as we find in the engineering process: Observe a situation; Plan a solution; Test the solution; Answer: “Did the solution work?”; Then REPEAT!
How Should I Implement a Continuous Improvement Initiative?
The steps are simple in concept. However, implementing a plan can be murky and uncertain.
When adopting and delivering a Continuous Improvement initiative, keep the following concepts in mind to ensure best practices are executed and your strategy yields success.
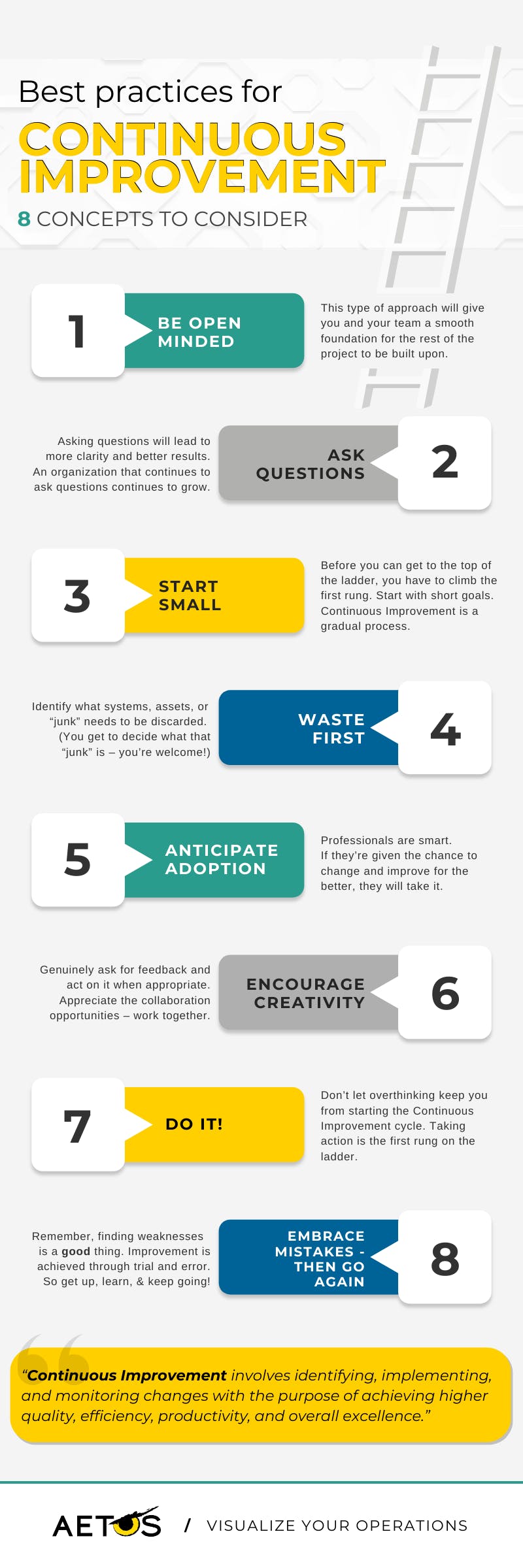
Be Open-minded:
The entire process is about seeking better solutions. In the beginning – and throughout the whole function – maintain an open approach. Which Continuous Improvement strategy is the most natural fit for your industry/needs? Would it give you the best results? What information or ideas should you suspend judgment on before jumping to conclusions?
This type of approach will give you and your team a smooth foundation for the rest of the project to be built upon.
Ask Questions:
The beauty of the Continuous Improvement mindset is found in the environment that it creates. Asking questions is a healthy indication of a thoughtful setting. Get comfortable (you and your staff) with intentional questions like: What strategies, tasks, or workflows are working well? Which ones could (or need to) improve? Where are we wasting resources? Who should help in this initiative? When should we start? Have any other organizations tackled the same problem(s)? Why is any of it important?
Asking questions will lead to more clarity and better results. An organization that continues to ask questions continues to grow.
Start Small:
Before you can get to the top of the ladder, you have to climb the first rung. Continuous Improvement is a gradual process, meant to naturally lead from one scenario to the next via a step-by-step process. Avoid making the big changes that are at the top of the ladder: you’ll get there soon!
Find and create short goals that will lead to the next iteration of the process. “You gotta score to win”, so get some easy, positive results.
Waste First:
Borrowing from the Kaizen Method, a best practice for Continuous Improvement involves eliminating waste before explicitly targeting improvement (which, in turn, will actually be a consequential benefit when done first). Where does your team waste time, money, resources, or opportunity?
Identify what issues need to be addressed or what “junk” needs to be discarded. (We’ll let you decide what constitutes as “junk” – you’re welcome!)
Anticipate Adoption:
Continuous Improvement strategies are structured to simplify processes; by starting small (with clear objectives) and giving your workforce initial success, your most competent personnel will see the value even before it has fully materialized. Remember, you’re all on the same team: when the business wins, everyone wins.
Professionals are smart. If they’re given the chance to change and improve for the better, they will take it.
Encourage Creativity:
It would be somewhat ironic if a Continuous Improvement initiative rigidly shut down the ideas of the hands-on individuals. By allowing your team to problem solve and ideate together at all stages of the process, you’re only strengthening the productive juices that power Continuous Improvement.
Genuinely ask for feedback and act on it when appropriate. Appreciate the collaboration opportunities – and keep in mind that the goal is for the organization to be more productive.
Do It!
Ok, you’ve read, researched, and explored enough. Now it’s time to try! Don’t let overplanning or overthinking get in starting the Continuous Improvement cycle. Take action and be encouraged that the first step in the ladder will help you get to where you want to be.
Then evaluate: How did it go? Where were you successful? Could anything be improved? Wait a minute….
Embrace Mistakes – then Go Again.
This mindset is cyclical, intent on revolving around the goal of productivity and efficiency. There will be hiccups; there will be failures. However, the Continuous Improvement process is a very welcoming place to failure and shortcomings – so long as that’s not where you stop.
Remember, finding weaknesses in a process or a system is a good thing. When that happens, embrace it. Effective teams are able to address the problems, strengthen the shortcomings, and look for more opportunities to improve and succeed.
Aetos & Continuous Improvement
Organizations around the world are constantly looking for ways to increase productivity and decrease inefficiencies. Whether that’s regarding safety, logistics, maintenance, regulatory compliance, onboarding & training, customer experience, or simply shipping more out the door, Continuous Improvement is a critical piece to thriving in competitive markets.
Aetos Imaging and our dynamic Visual Maintenance Management System (VMMS) is granting companies a rapid, revolutionary platform to embrace and enable a Continuous Improvement mindset. By leveraging 3D imagery, our clients are seeing incredible use cases for visualizing their operations and making their processes more productive.
Aetos is built on the Continuous Improvement perspective. Innovation and disruptive technologies alike are rooted in an intentionally open mindset and a desire to ask questions.
How would onboarding and training improve if it was conducted in a site-specific, virtual replica of the environment being serviced? In what ways would remote collaboration between teams and departments be enhanced with native video conferencing layered with visual context? How would an industrial plant change if their entire asset inventory, history, and live network status was completely accessible at a literal glance?
These musings – and many others – were our starting foundational questions. Since then, Aetos has made considerable strides forward in understanding our industries and supporting our clients.
The aforementioned concepts and framework will continue to drive our operations. Aetos is committed to continuous, intentional improvement and innovation for better, safer, more efficient environments.
Want to see a Demo of our dynamic platform for the built environment and its operations? Contact Aetos today to experience the world’s first VMMS – demo@AetosImaging.com