Embrace the Future of Maintenance with Aetos
The general public admires the external appearance of large buildings. Facility managers - and those intimately connected with the built environment - focus on the intricate workings within.
Organizations around the world are being asked to solve more complex problems with less support: like cutting energy use across a portfolio or training new staff without having enough critical data or operational clarity to execute.
Inevitably, equipment errs and machinery malfunctions, leaving Facilities Managers (FMs) with the task of providing a solution for their assets and workers.
Is Preventative Maintenance "Outdated"?
Preventative Maintenance (PM) involves regular, planned maintenance activities aimed at mitigating breakdowns and failures of equipment. The goal is to keep assets in optimum operating condition and extend their useful life.
In industries like healthcare, manufacturing, and commercial real estate, preventative maintenance can be crucial for not only sustaining operations but also ensuring safety and compliance with various regulations.
Organizations and their teams are asked to do more with less. In the past, preventative maintenance practices have significantly assisted facilities in keeping their equipment running well and not employing a "run to fail" maintenance approach.
Effective PM aims to reduce the need for corrective maintenance and the costs associated with equipment downtime as the age-old challenge of efficiently managing maintenance tasks while minimizing downtime persists.
However, preventative maintenance tasks assume the asset in question is in need of services (and also assumes the asset will be put back together perfectly).
But what if the asset doesn't need to be serviced yet?
What if production needn't be interrupted with a scheduled task?
What if there was a way to enhance asset production while further extending the lifespan of the equipment at hand?
These three questions point to a need for more information and more operational data. The answer: digital transformation for performance monitoring and data management.
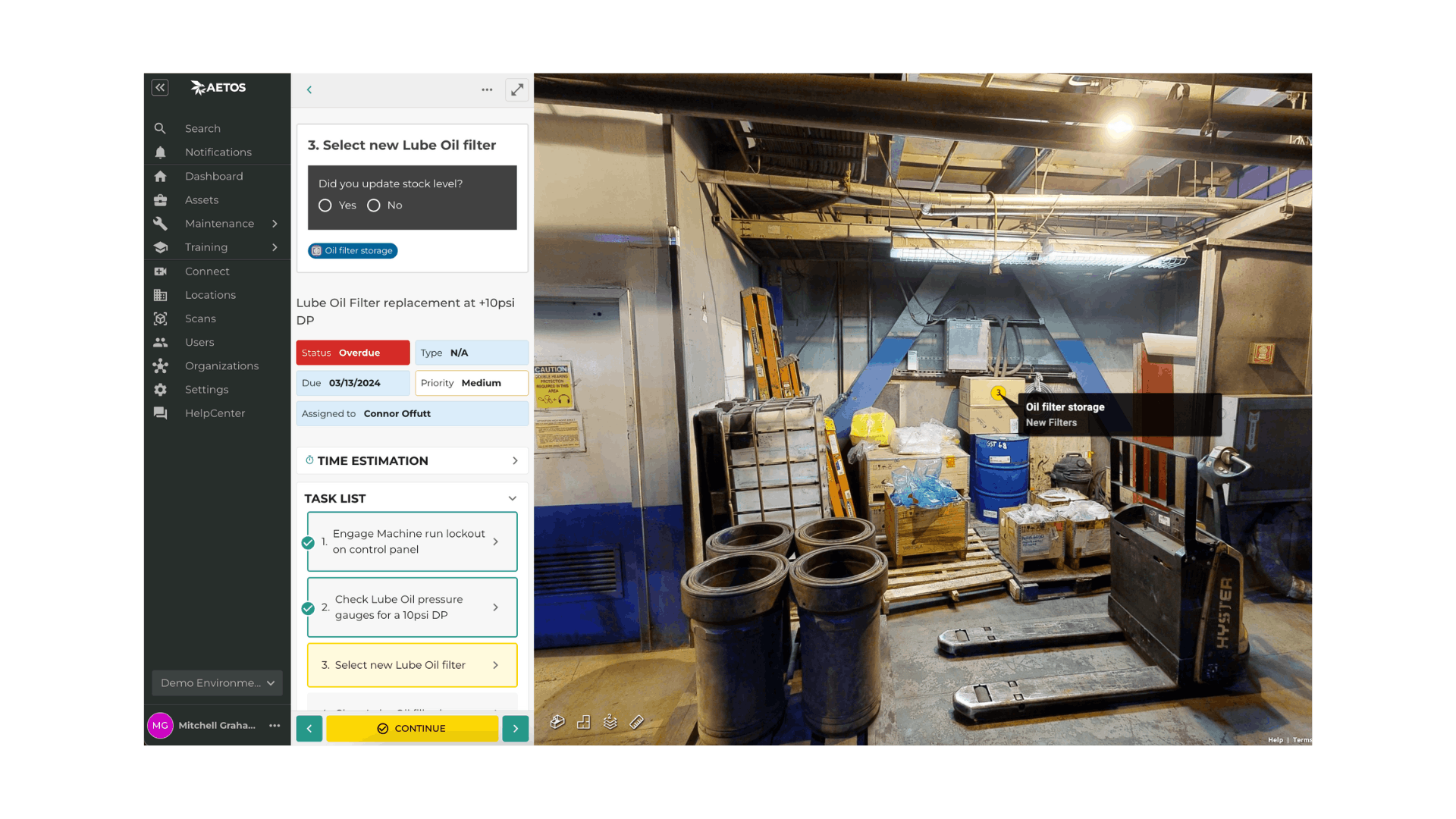
Better Data = Better Operations
Downtime is a costly enemy. Unplanned maintenance can disrupt production, lead to significant financial losses, and affect the overall efficiency of a facility.
Sometimes this downtime is a result of poor monitoring; sometimes this downtime is a result of inefficient execution on the production line (which also leads to more waste).
Better data and operational excellence can lead to predictive maintenance capabilities – a transformative approach to asset management that not only prevents downtime but also predicts opportunities for optimization.
Like previously mentioned, preventative maintenance involves regular, planned maintenance activities to keep equipment in top working condition. It’s a proactive approach that can prevent unexpected failures and extend the lifespan of assets.
But imagine having a system that allows maintenance teams to schedule tasks based on how an asset is performing.
With live IoT integrations and monitoring, production teams can do just that.
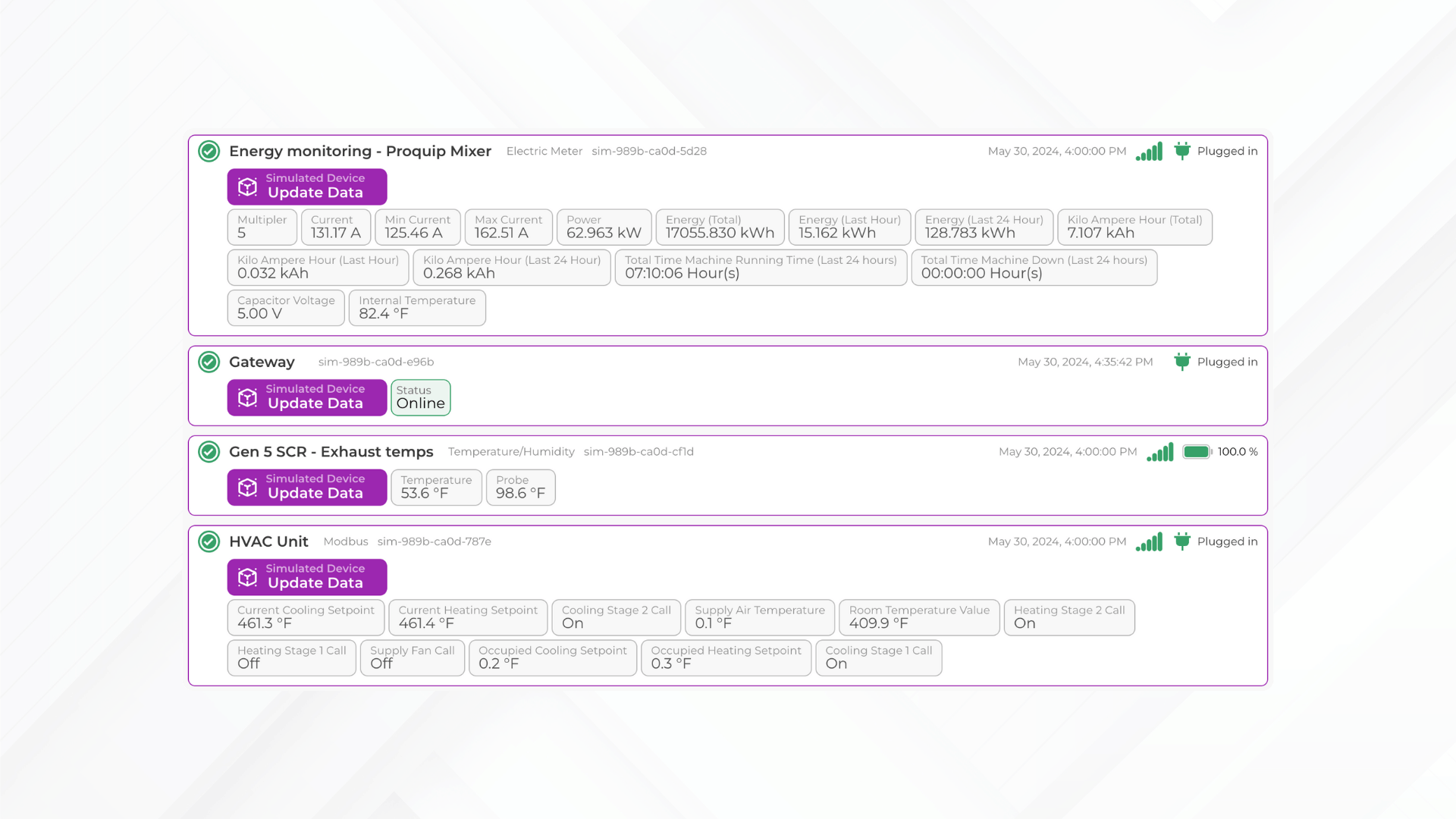
Predict Opportunities with Predictive Maintenance
Predictive maintenance takes asset management to the next level by using data and analytics to predict when maintenance should be performed. This approach reduces the frequency of maintenance tasks, saving time and resources, and ensuring that interventions are only made when necessary (and at opportune times for any particular industry).
Aetos harnesses the power of predictive maintenance through IoT integration. Wireless sensors connect equipment to the digital world, providing continuous data on performance and condition. This integration allows for precise monitoring and predictive analysis, greatly impacting the performance of a production line or the energy usage of certain assets.
Our platform consolidates all maintenance data and tools into a single interface, simplifying management and enhancing visibility, making it easier to monitor the health of all assets in real-time. This foresight enables maintenance teams to act before problems occur, reducing unplanned downtime and optimizing operations.
Positioning operations with visual context, our platform captures and delivers data to predict potential failures and maintenance needs based on predetermined metrics and thresholds.
And to take things even further: Condition-Based maintenance is made possible by capturing live performance to mitigate immediate mistakes, misalignments, and malfunctions.
Similar to predictive maintenance, condition-based maintenance leverages live data for actionable insight. Although both use sensors and data for informed decisions, the main difference between the two is found in the rate of response; essentially, predictive uses operational data to plan maintenance decisions in the future whereas condition-based maintenance uses operational data to solution more immediately.
Both practices of using performance data for predictive maintenance and troubleshooting immediately with condition-based maintenance can lead to significant cost savings, reduced downtime, and better overall production.
And both practices are possible with Aetos.
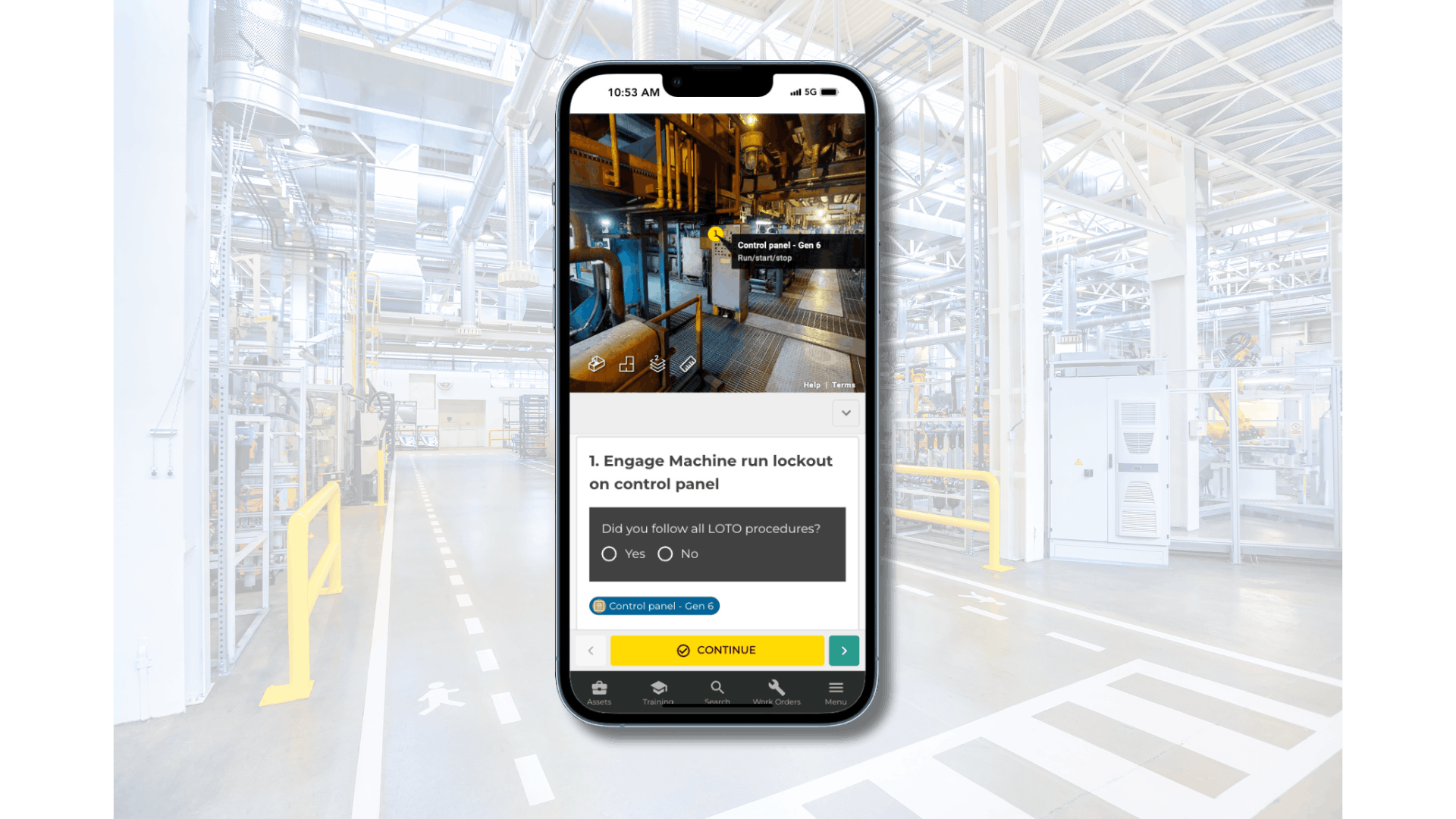
Unlocking ROI - The Numbers Don't Lie:
- 20% Reduction in Maintenance Costs: Facilities using Aetos preventative maintenance feature have reported a substantial reduction in maintenance expenses within the first year of implementation.
- 25% Decrease in Unplanned Downtime: Real-time monitoring and early issue detection mean less downtime, fewer disruptions, and more productive hours.
- 30%+ Improved Technician Efficiency: With guided work orders and visual instructions, technicians experience increased efficiency and effectiveness, translating to more tasks completed in less time. Some FMs even reported a percentage as high as 50%!
- 40% Increase in Asset Lifespan: Well-maintained assets lead to a longer lifespan, and our proactive approach ensures optimal performance and longevity – reportedly up to 40% from some of our users.
- 50% Decrease in Onboarding Technicians: Although seemingly tangential to PM operations, facility managers have reported a significant drop in the time it takes to onboard field-ready technicians, yielding smoother PM tasks and management.
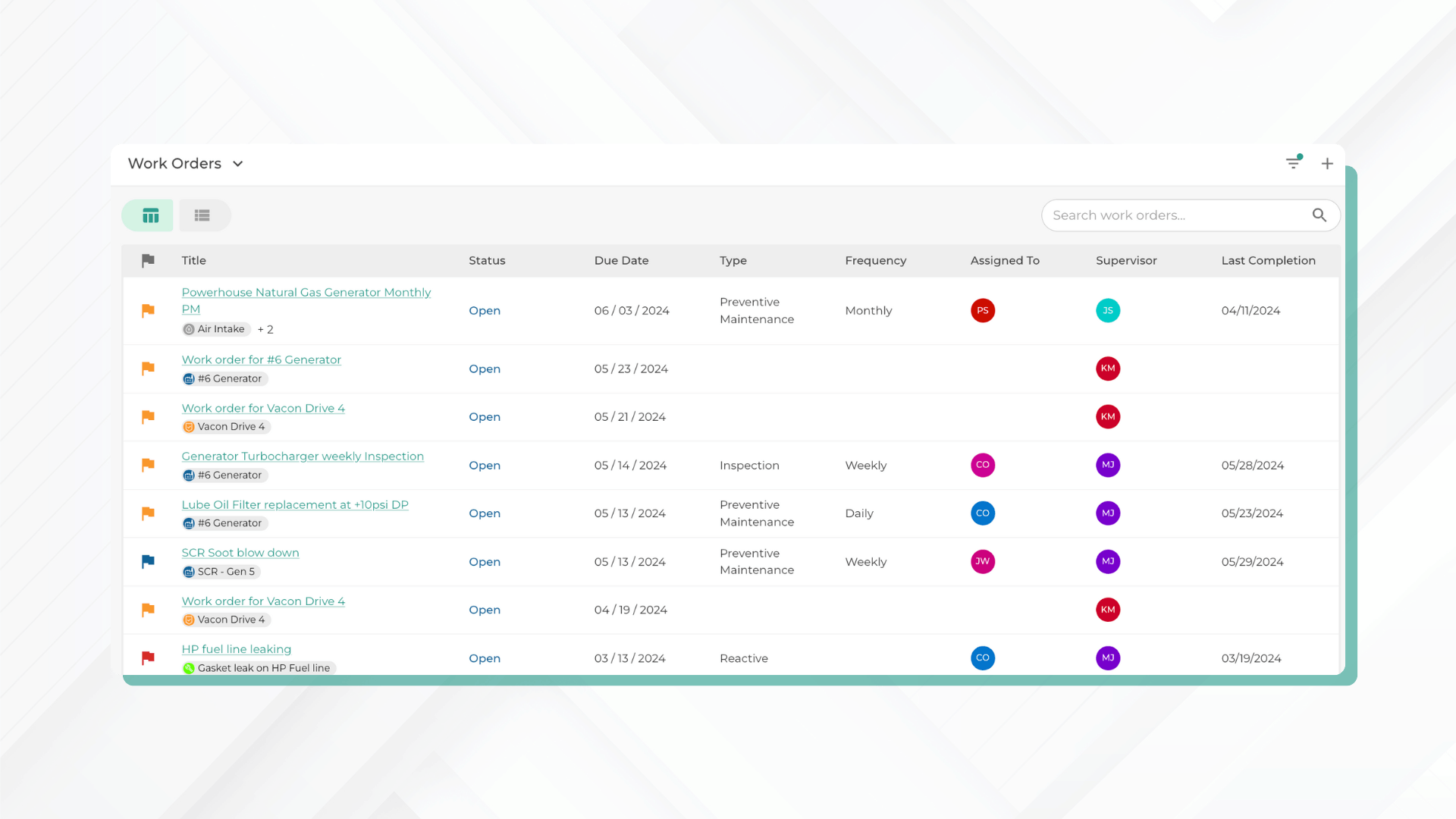
Embrace the Future of Maintenance:
By transforming the traditional – often reactive – PM approach into a proactive, data-driven one, Aetos is setting new standards in facility management and operation. (And in case it’s news to some, we are championing sustainability and compliance goals for better buildings and a better world.)
Organizations can make the jump to Industry 4.0 and the transformative PM platform with a solution that simply delivers more support, precision, and assistance to on-site technicians and FM decision makers.
Imagine having the power to visualize, manage, and maintain your entire facility from the palm of your hand.
With Aetos, that vision is a reality.
As a best-in-class Visual Maintenance Management System (VMMS), we partner with facility managers to transform their maintenance operations from reactive to proactive, predictive, and even conditions-based capabilities. Many organizations already have these initiatives in place, but don’t quite have the tool to get them over the line.
We are intent on realizing company initiatives centered around shifting to a better way of maintenance.
This shift not only prevents costly downtime but also identifies opportunities for improvement, driving efficiency and productivity across a production line, comprehensive facility, or entire portfolio.
Embrace the future of asset maintenance and take the next step in optimizing your operations today.
Worth a chat? Contact Aetos today and find out more on how a powerful VMMS can change the way your facilities leverage data for better maintenance.