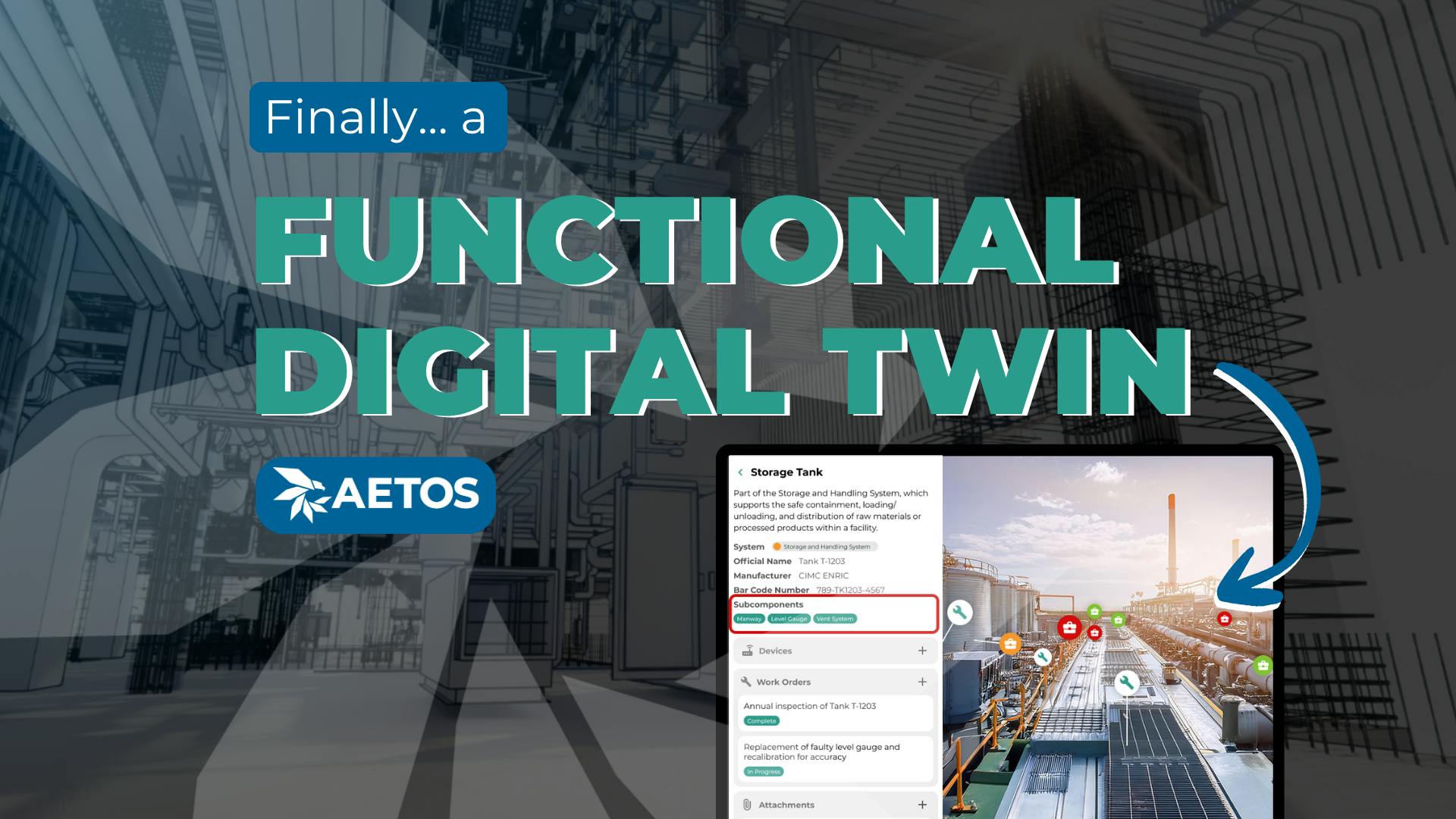
Finally, a Functional Digital Twin.
August 04, 2025
Continue reading ➔
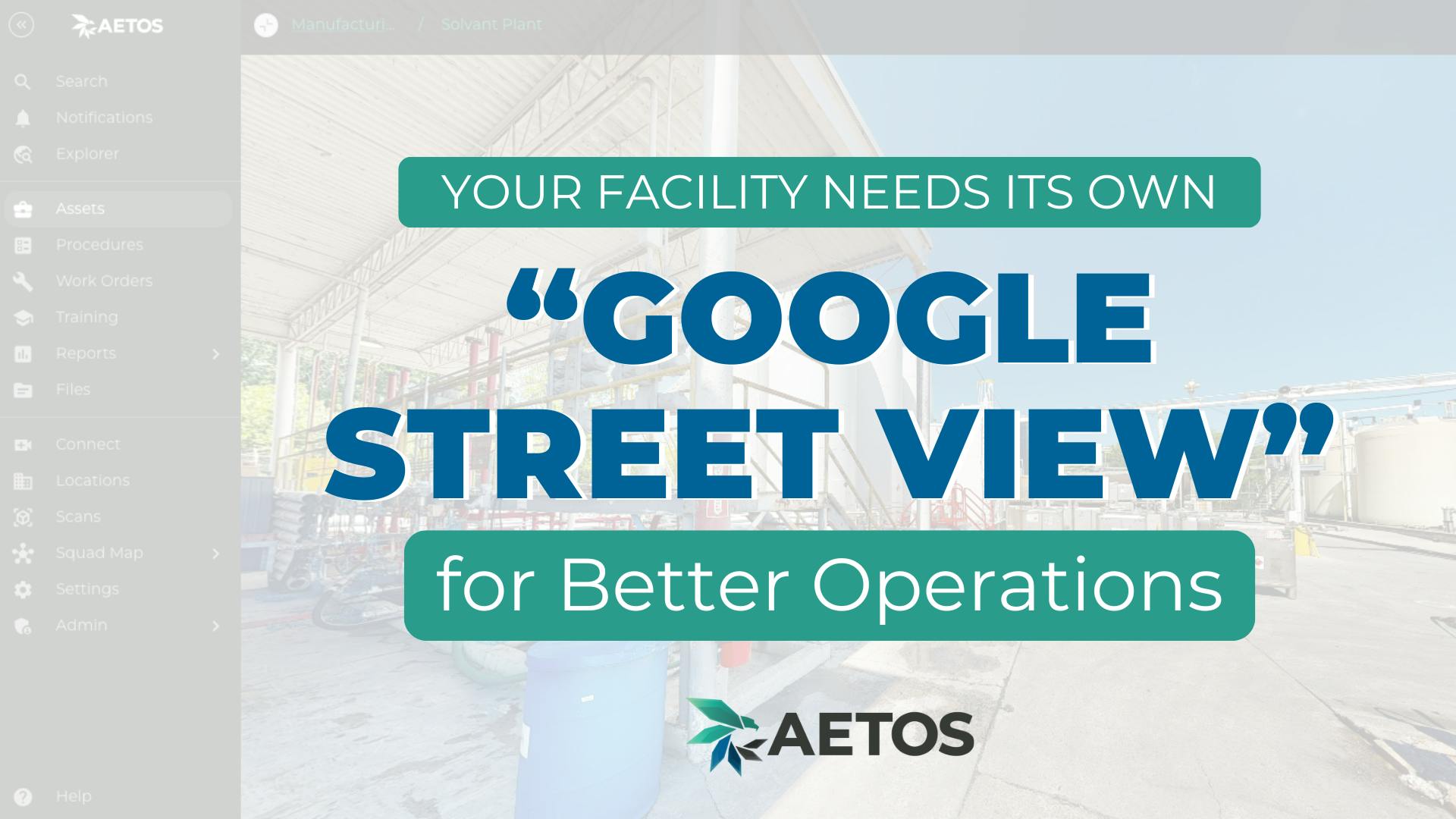
Why Your Facility Needs Its Own “Google Street View” for Operations
July 01, 2025
Continue reading ➔
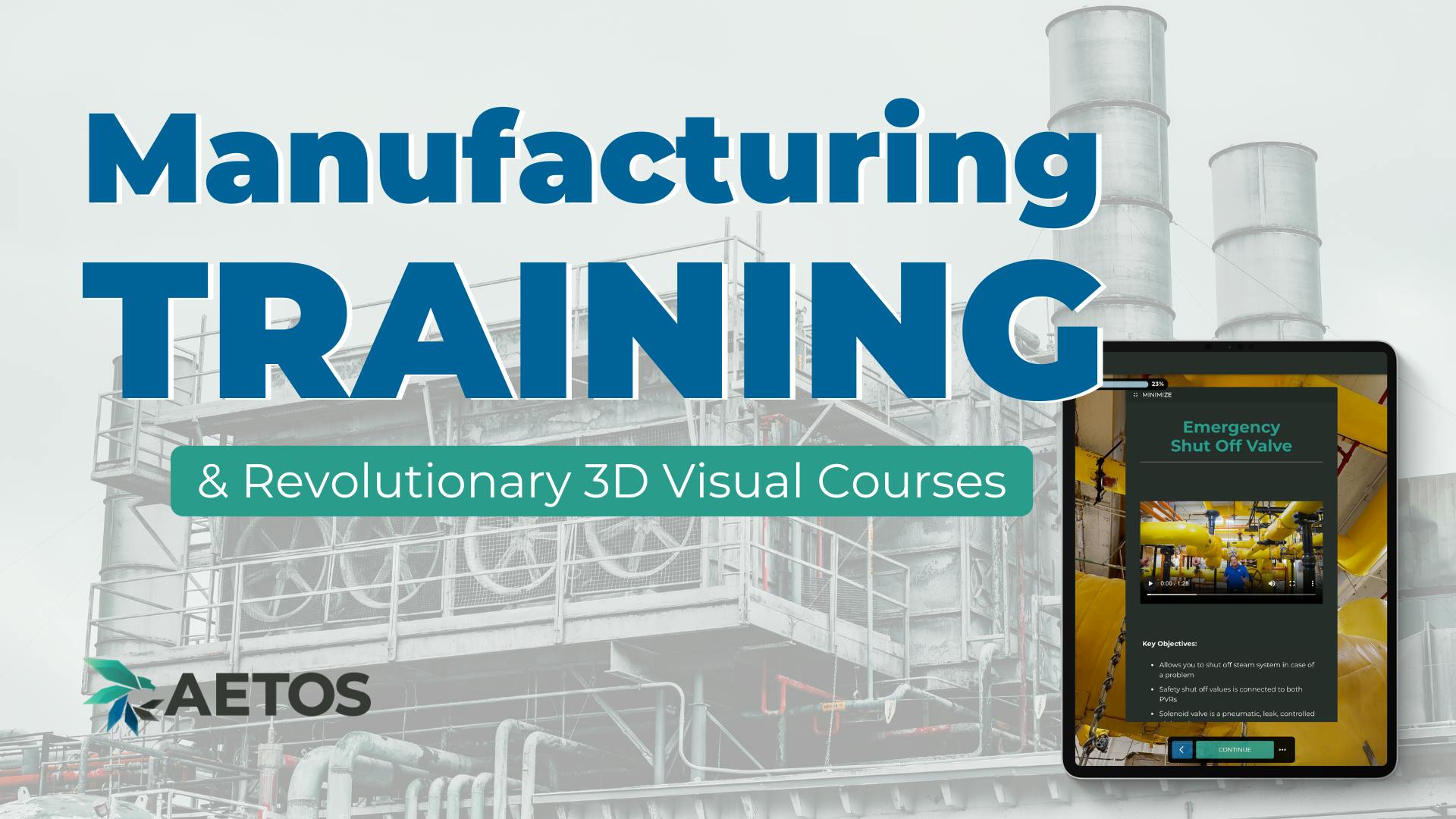
Manufacturing Training: Revolutionary 3D Visual Courses
January 28, 2025
Continue reading ➔
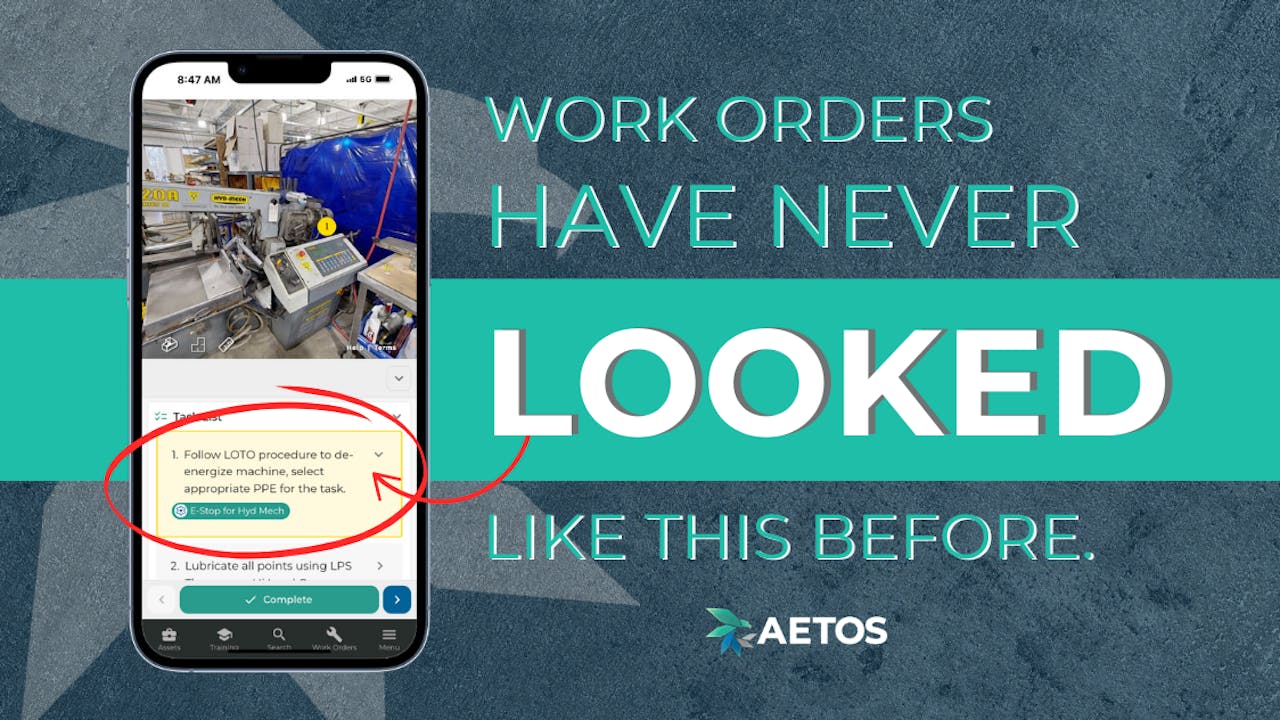
Work Orders Have Never Looked Like This Before
December 06, 2024
Continue reading ➔
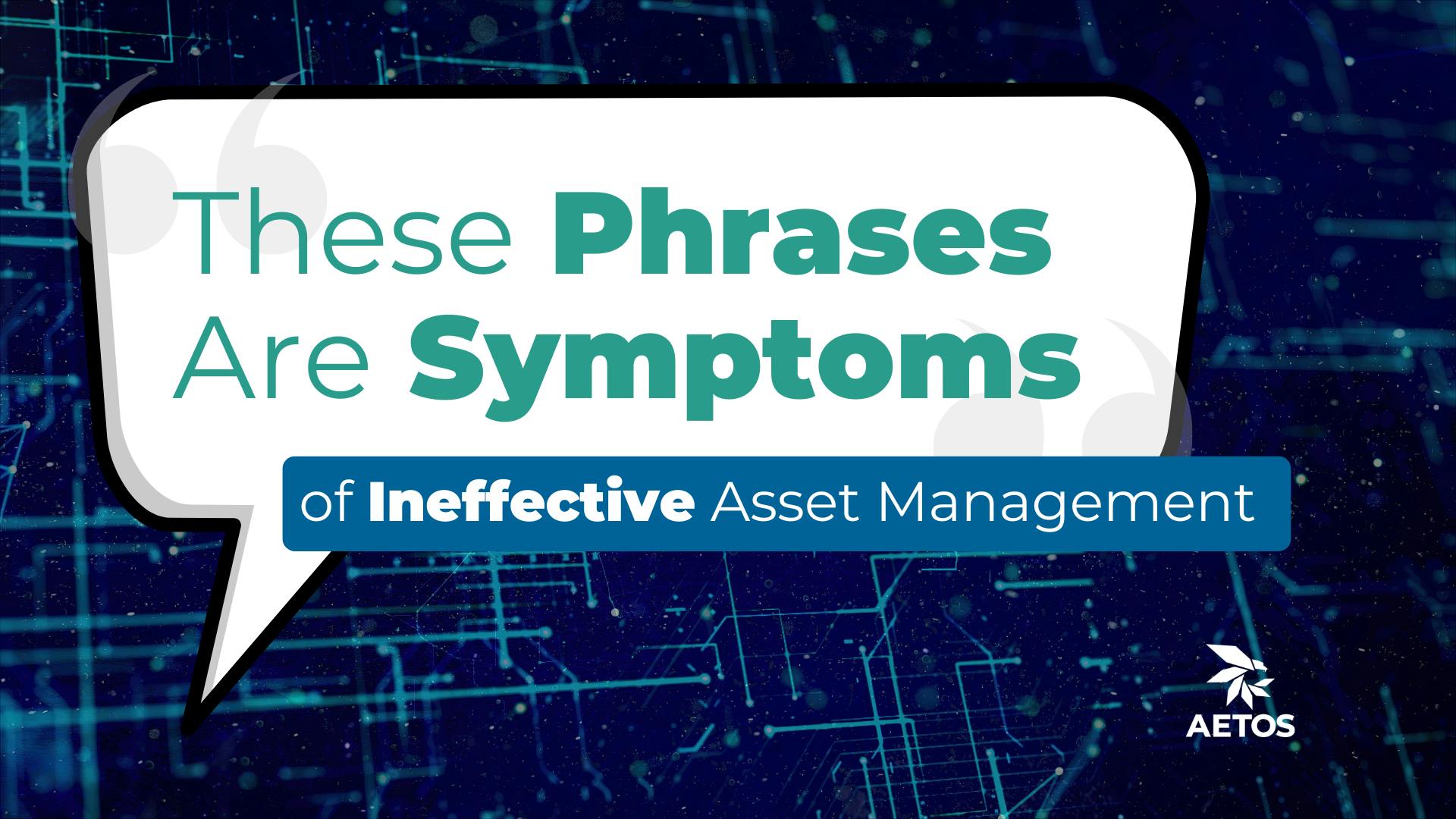
These Phrases Are Symptoms of Ineffective Process Management
October 17, 2024
Continue reading ➔
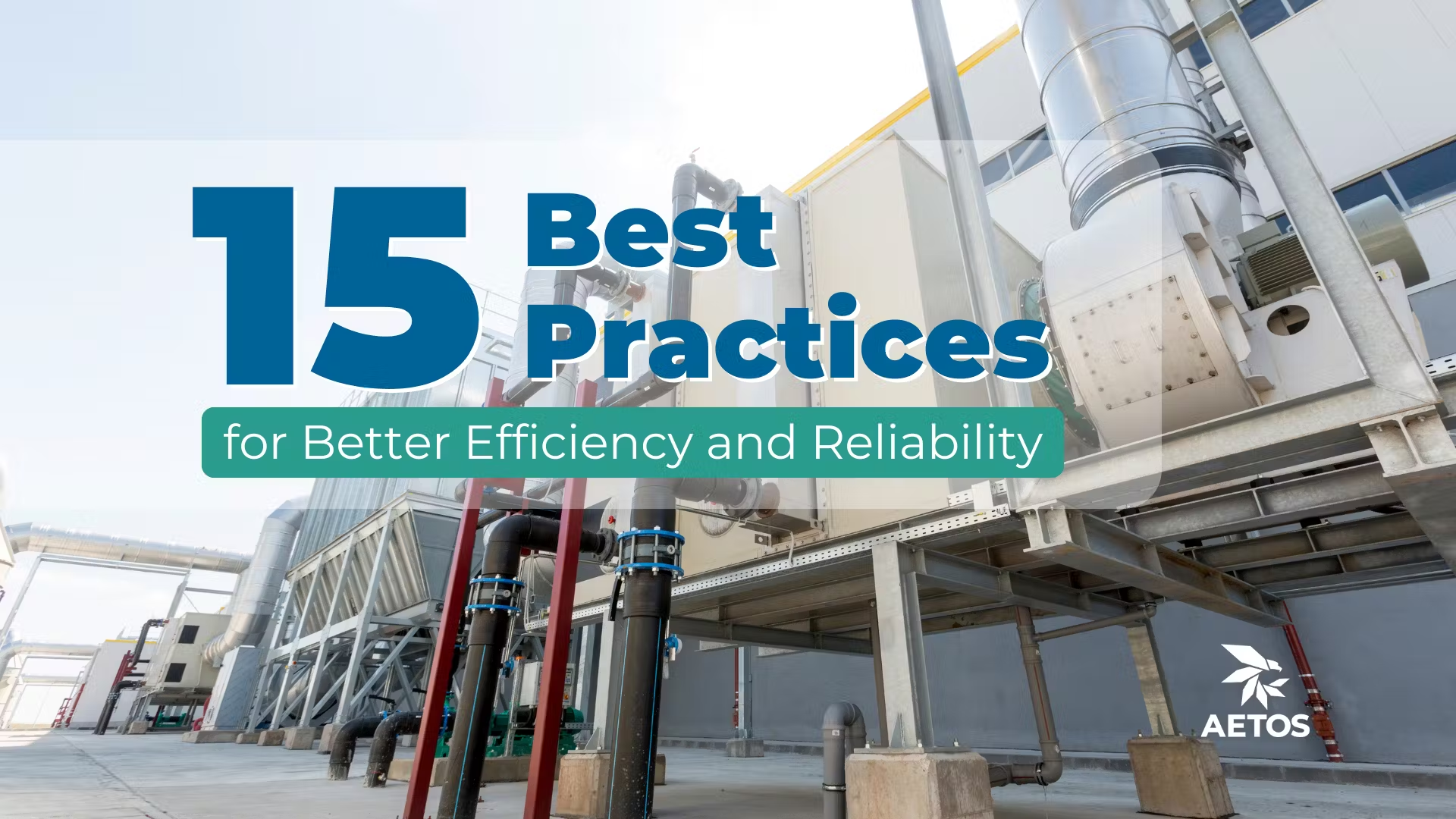
15 Asset Management Best Practices for Better Efficiency and Reliability
September 18, 2024
Continue reading ➔
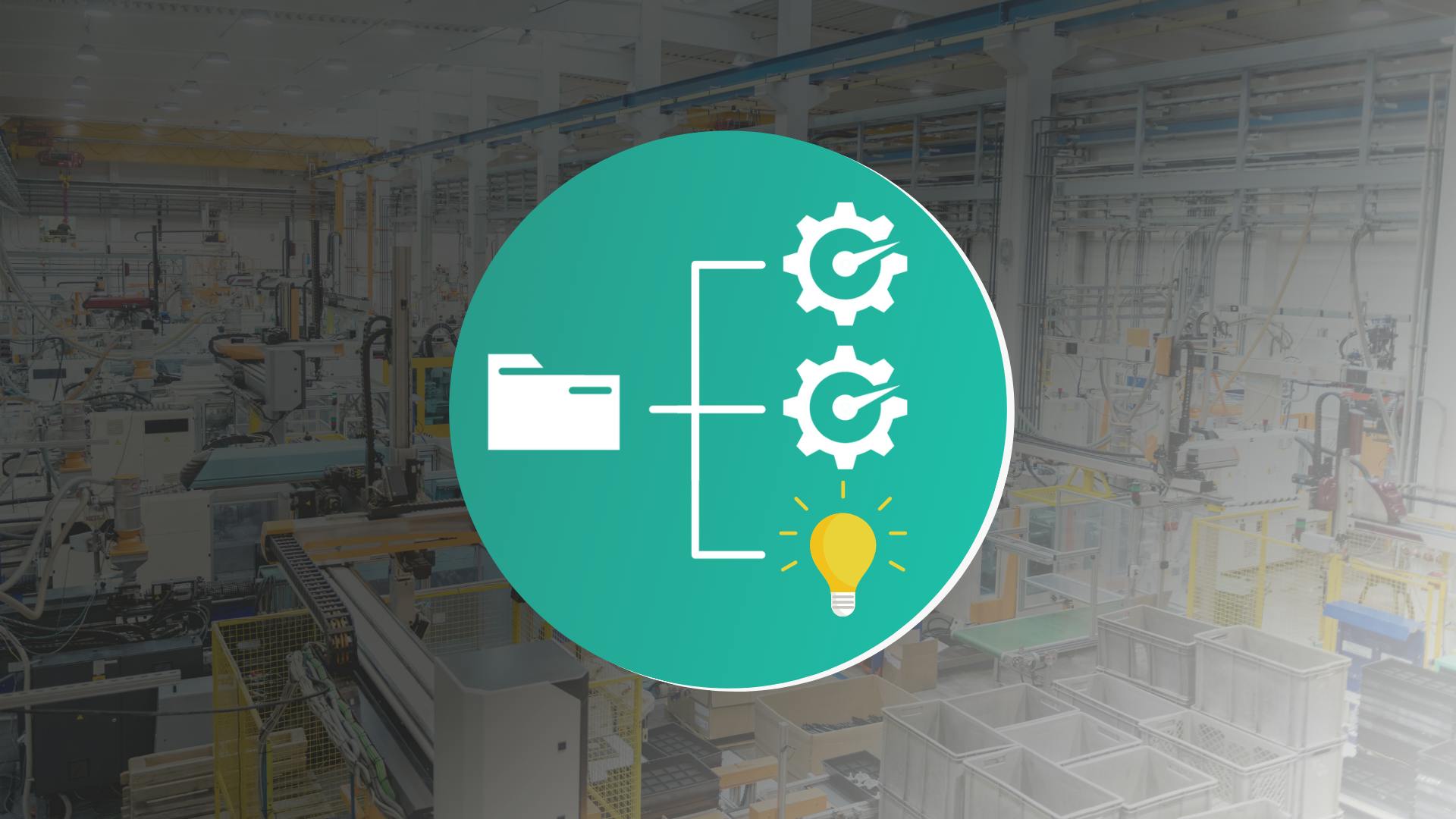
Illuminate Facility Operations with Efficient Asset Management
August 31, 2024
Continue reading ➔
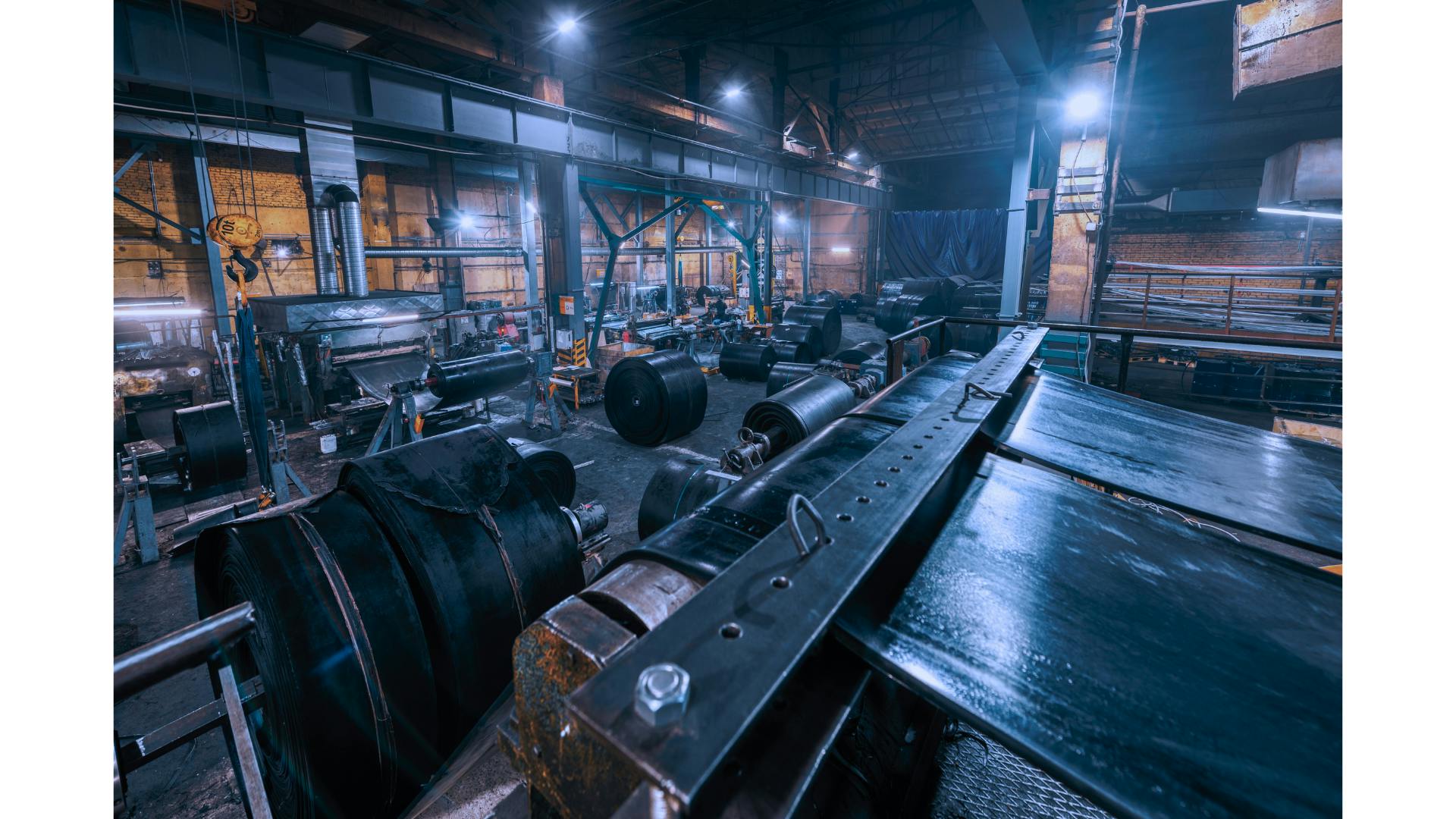
A Looming Crisis: The Widening Knowledge Gap in Facility Management
August 01, 2024
Continue reading ➔
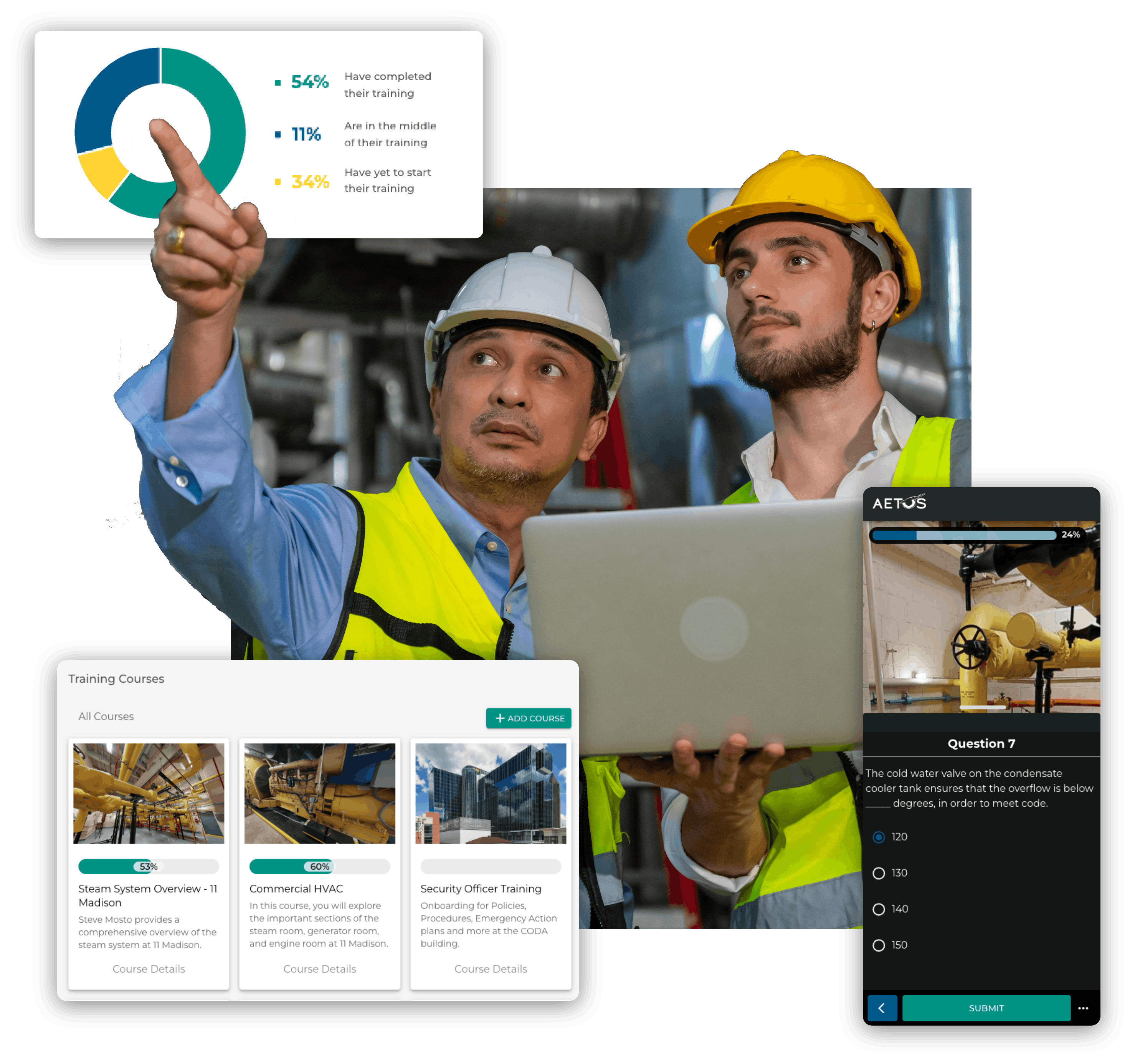
Unparalleled Clarity for Training & Compliance: 7 Reasons to Leverage Your Digital Twin for Employee Training.
July 12, 2024
Continue reading ➔
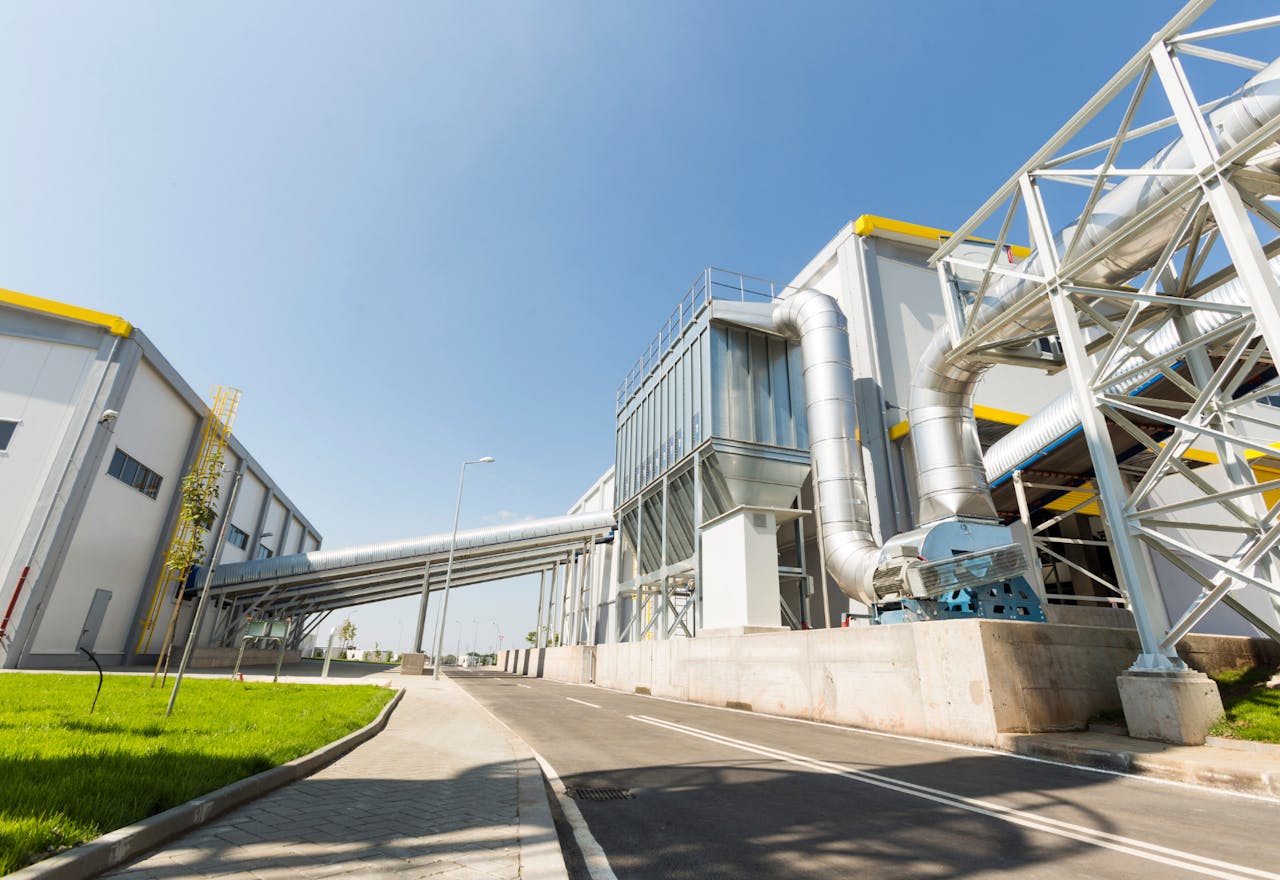
Enhancing Energy Management & Cost Savings with Aetos Imaging
June 10, 2024
Continue reading ➔