A Looming Crisis: The Widening Knowledge Gap in Facility Management
The manufacturing industry has experienced a resurgence in the United States.
Infrastructure repairs, climate change initiatives, tax reforms, domestic investment, and energy security are some of the overarching reasons why this resurgence is occurring. The COVID-19 pandemic also played a significant role in the uptick in manufacturing in the U.S. due to economic and geo-political factors.
“American manufacturing growth outpaced the rest of the world’s at the end of 2022,” according to GeniusERP.com. “Additionally, in 2022, for the first time since the late 1970s, U.S. employment in manufacturing surpassed the peak set during the previous business cycle.”
And in 2023 alone, the manufacturing sector contributed $𝟐.𝟖𝟗 𝐓𝐫𝐢𝐥𝐥𝐢𝐨𝐧 to the U.S. GDP, amounting to 𝟏𝟎.𝟑% of total GDP.
Recent years have seen a boost in manufacturing within the United States. Companies are reshoring operations to improve supply chain resilience and reduce dependency on foreign manufacturers.
According to ReshoreNow.org, 2021 yielded more than 260,000 jobs brought back to the U.S., marking the highest annual rate in history. This trend is expected to continue, fueled by technological advancements and governmental support.
That means 260,000 techs were trained and onboarded in 2021. There was a knowledge transfer that needed to happen for each of those new workers. It goes without saying that this number will continue to go up as the industry grows.
Manufacturing is clearly here to stay. What isn’t so certain is the workforce needed to run these facilities.
It’s getting harder for organizations to fill employment gaps, as well as to transfer operational knowledge to the next line of workers.
The looming crisis is thus: will there be enough workers – or better technology advancements – to keep pace with this resurgence?
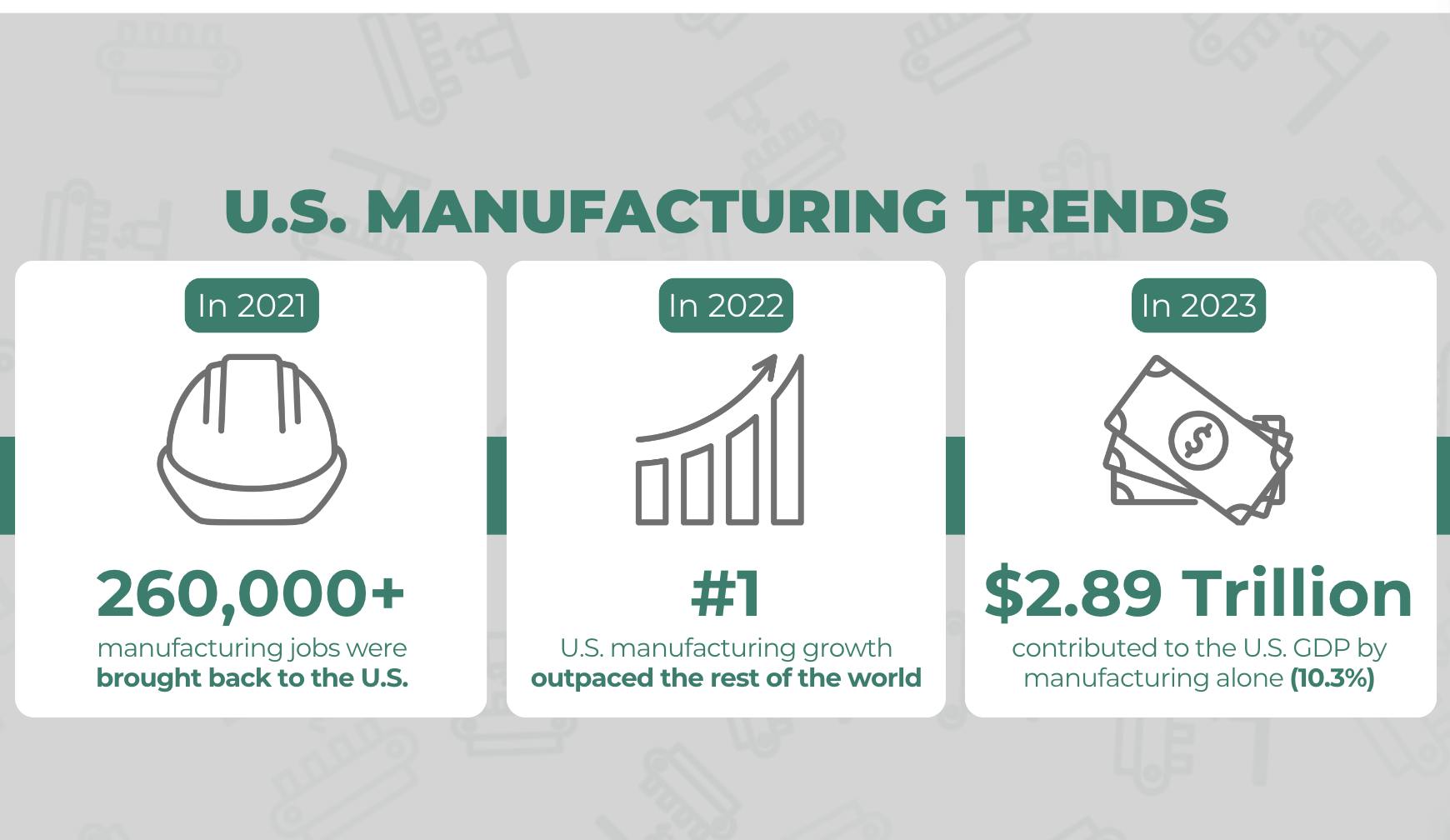
More Jobs, Yet Less Workers
Although the increase in manufacturing is fantastic news for the domestic economy, the facility management sector faces an unprecedented challenge: a widening knowledge gap in institutional knowledge and technical know-how between their seasoned techs and their new hires.
Facilities need proficient workers. Regardless if organizations are battling fewer workers or less experienced technicians, facility teams are desperate to find sustainable ways to grow their workforce without compromising production.
New personnel will always have a learning staircase to climb before they’re considered proficient employees. The workforce is playing a game of keep-up, and it will only continue to be more challenging as facilities grow.
There are many variables that could contribute to the widening gap, ranging from competitive opportunities to digital competencies to generational factors – just to name a few.
The same GeniusERP article goes on to state, “Roughly 200,000 to 250,000 new manufacturing jobs are expected to be added in the U.S. over the next couple of years, with millions more likely to be added over the next decade.”
That’s a lot of jobs.
And a lot of onboarding.
Net-new opportunities are becoming more available with the expansion of U.S.-soil industrial growth. Yet as job opportunities become more prevalent, they’re not always guaranteed to be filled.
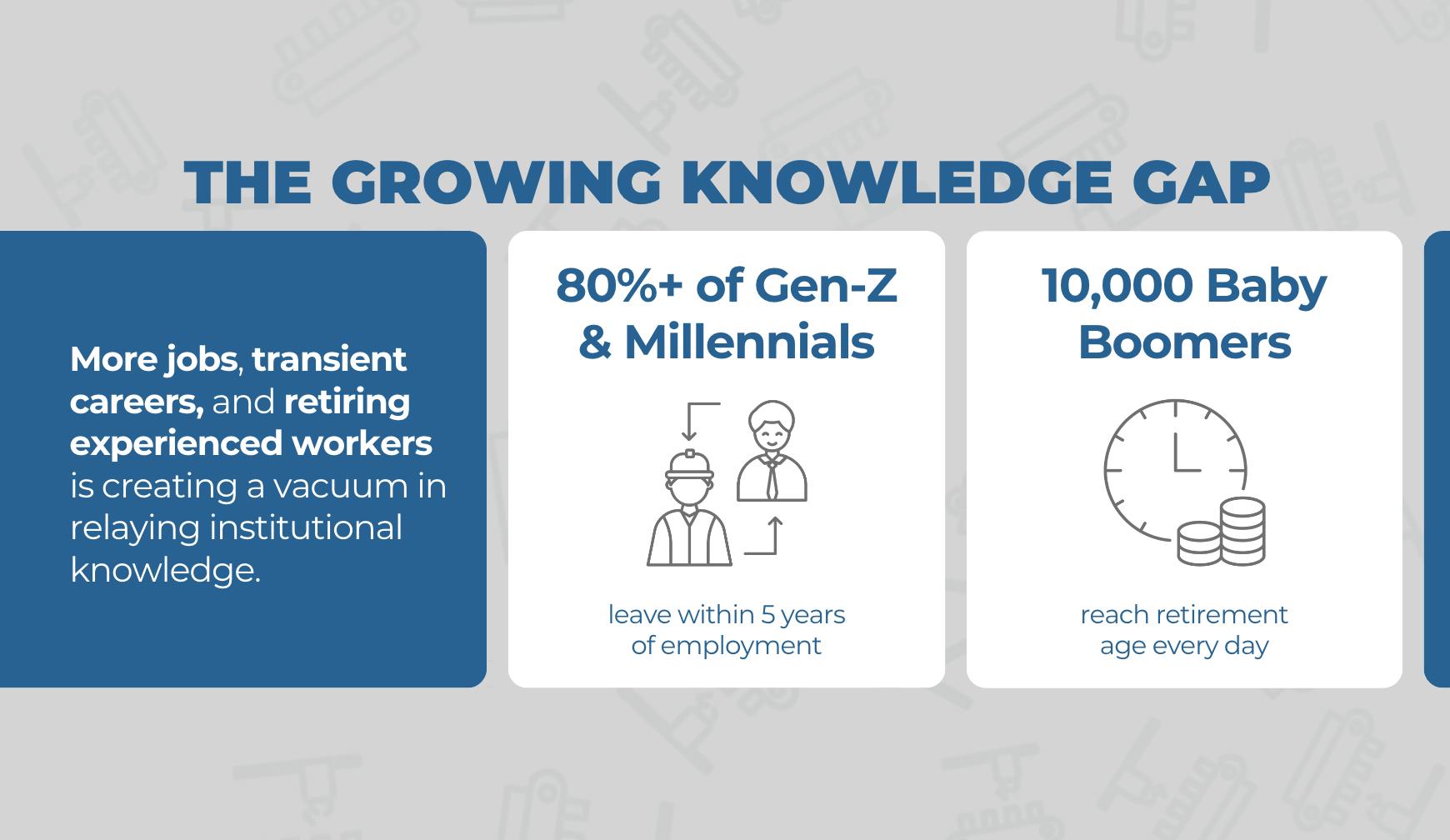
Transient Careers
There’s a growing trend with the younger generations of workers as it pertains to career commitments: on average, less than 20% of Millennials & Gen Z plan to stay for 5 years or more at their current job.
Some would consider this to be significant churn for a growing industry.
More churn leads to slower growth, more in-depth onboarding time, and more position shuffling. And if it takes an entire year to onboard a worker, most younger employees are close to being 20% done (or more) with their time in the organization – mathematically speaking.
Organizations must train their workers. But the way onboarding occurs within manufacturing settings may be outdated and too slow.
As younger workers begin to fill these job opportunities, there’s strong statistical evidence that they will no longer be around for their 10-year anniversary – quite a change from the more consistent generations before them!
The Retirement of Baby Boomers
Months ago, we chatted about the retiring workforce and how senior technicians are leaving faster than their replacements are ready to fill their shoes.
The Baby Boomer generation, born between 1946 and 1964, has long been the backbone of the facility management workforce. Their extensive experience and knowledge have been critical to maintaining and optimizing manufacturing facilities.
However, as they approach retirement age, a remarkable exodus from the workforce is now inevitable. Pew Research notes that approximately 10,000 Baby Boomers reach retirement age every day.
Now, not every Boomer retires when they reach retirement age, but this “when-not-if” scenario is creating a looming crisis in capturing and delivering best practices and site-specific expertise.
When that knowledge eventually walks out the door, it’s gone.
How can organizations capture and preserve their institutional knowledge? How can technical know-how be efficiently delivered to the next generation of workers?
Gap Implications for Facility Management
The convergence of these factors – an increase in job openings, transient young workers, and retiring Baby Boomers – has imposing implications for facility management.
With more facilities to manage and fewer experienced professionals to oversee them, the knowledge gap widens.
As any manufacturer knows, outputs are determined by inputs.
Current instructional methods are not keeping pace with the industry. Knowledge transfer inefficiencies, onboarding times, and retiring pros are contributing to uncertainty.
While knowledge gaps stem from the retirement of seasoned Boomers and a decline in long-term job commitments among younger generations, how can organizations – particularly ones in growing industries like manufacturing – combat the uphill battle of onboarding, training, and retaining their talent?
Since all workers need to be onboarded and trained, could creating better, faster learning processes help personnel – and by extension, organizations – operate at their potential sooner?
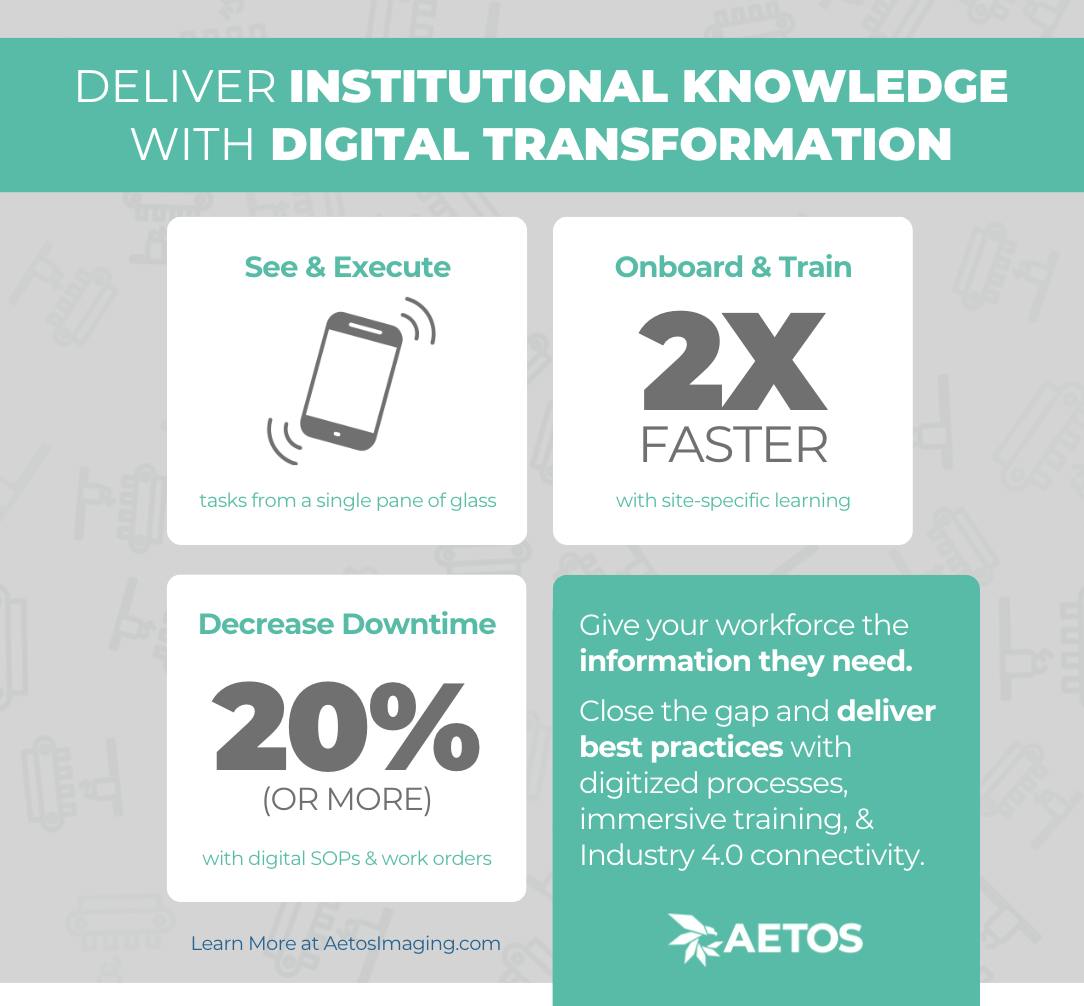
Digital Transformation to the Rescue
Let’s revisit those factors again. More job openings, exiting Boomers, and an influx of younger workers may yield the “perfect storm” for adopting digital transformation.
Digital transformation, according to Enterprisers Projects, is “the integration of digital technology into all areas of a business, fundamentally changing how you operate and deliver value to customers.”
It’s the process of leveraging Industry 4.0 connectivity and data capture for more streamlined, accurate, and sustainable operations. (Sound like a mouthful? Check out our blog that explains these nuanced industry terms.)
Necessity drives innovation. And right now, with the current landscape of managing a workforce in a growing sector with (seemingly) diminishing human resources, digitizing processes and making critical procedures more intuitive, accessible, and efficient is an effective strategy for facility teams.
Digital transformation is not replacing the workforce with robots. It’s enhancing employee productivity with better methods, data, connectivity, efficiency, safety, and support.
This transformation looks like using more immersive learning environments to expedite learning and improve knowledge retention without compromising on compliance.
It looks like monitoring and harnessing real-time data – IoT or otherwise – to make more informed decisions.
It looks like observing, managing, and maintaining a specific facility from a single pane of glass.
It looks like true innovation: capturing and delivering institutional knowledge and business processes so entire organizations can operate with more clarity, connection, and confidence.
Close the Gap & Grasp the Opportunity
It’s reasonable to state that knowledge gaps are normal. As an industry grows, so does opportunity within that sector.
However, this looming crisis can cause considerable challenges for organizations as they look to navigate uncharted trends. Retiring professionals, transient workers, and a desire to grow with the industry all contribute to the complexity of asset and personnel management.
And yet, there may be a solution that proves revolutionary for facility teams.
Effectively and efficiently instructing new workers is a growing necessity. Old methods simply are not fast enough to keep up, nor are they reliable and sustainable as equipment and technologies improve.
By leveraging a VMMS (Visual Maintenance Management System), facility teams, workers, and upper management alike can leverage visibility for better operations.
Could digital transformation help companies fill these knowledge gaps faster and keep pace with growing trends across the industry?
Digitally transforming operational processes – like training, SOPs, or even work order support – could be the strategy to avoid this looming crisis and grasp the opportunity at hand.
There’s no doubt the gap exists. It’s up to each organization to decide whether that gap grows or shrinks.
Grow with the industry and don’t get left behind. Close your knowledge gaps with site-specific training. Learn more at AetosImaging.com
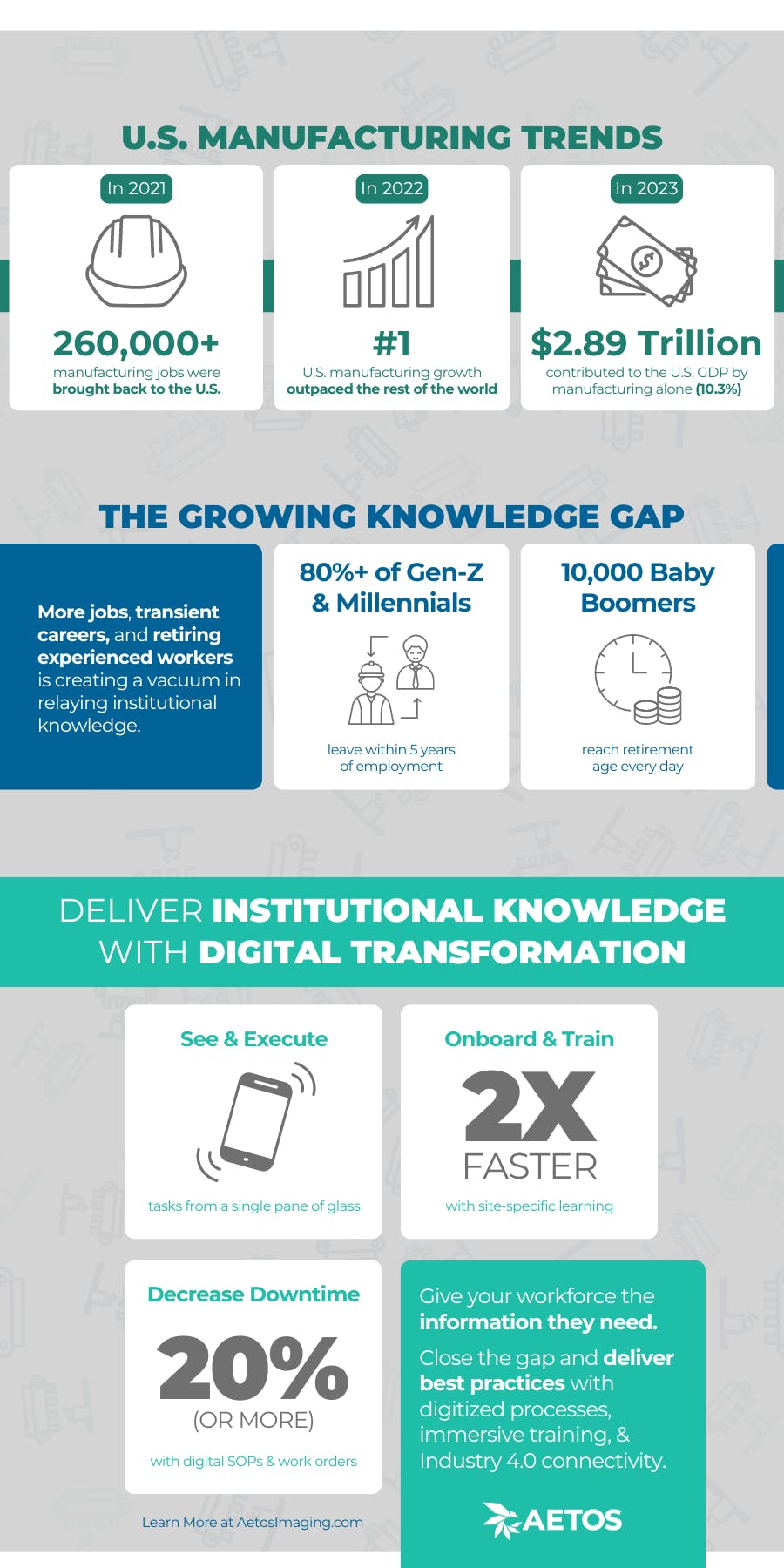