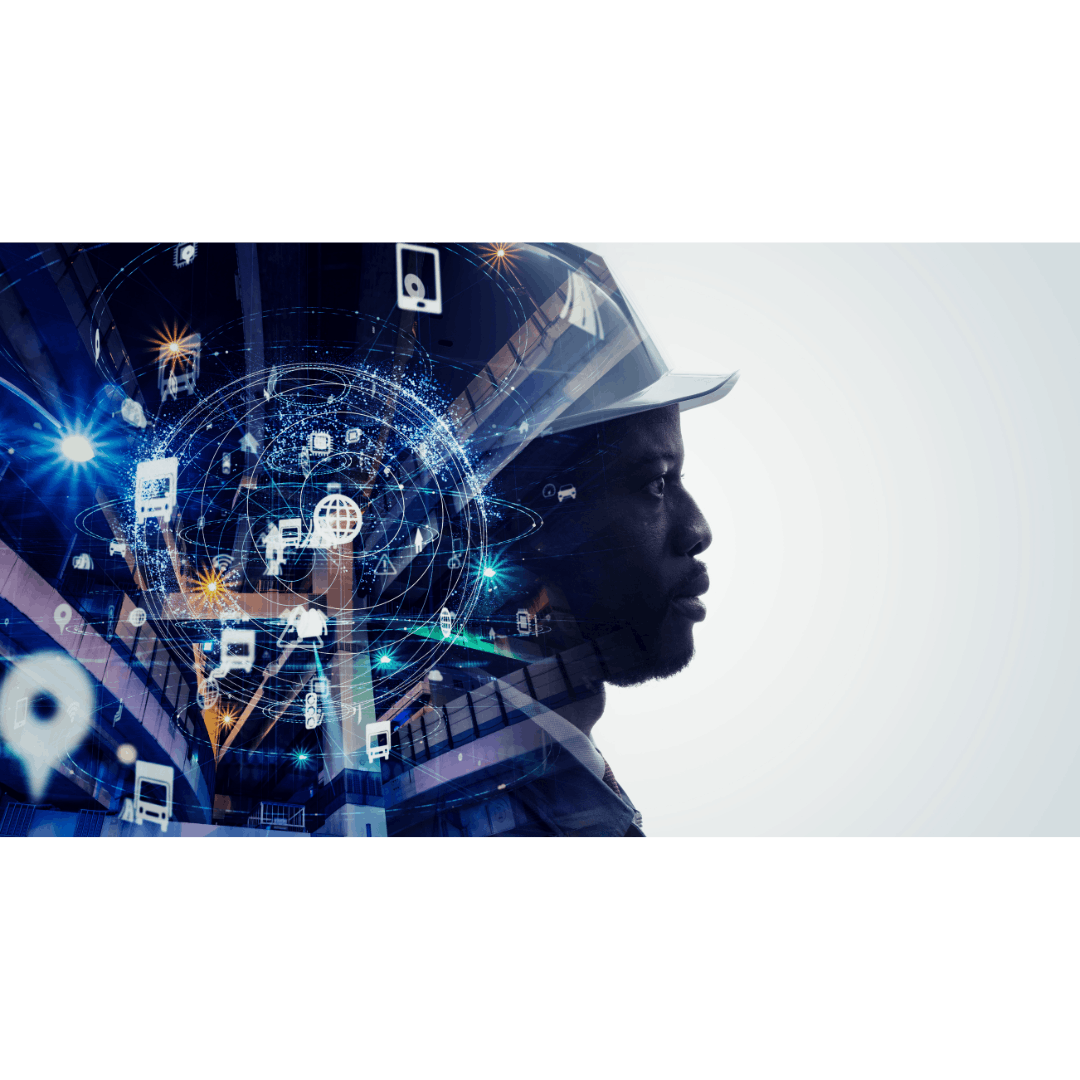
What Is VMMS? And Why Now?
June 04, 2025
Continue reading ➔
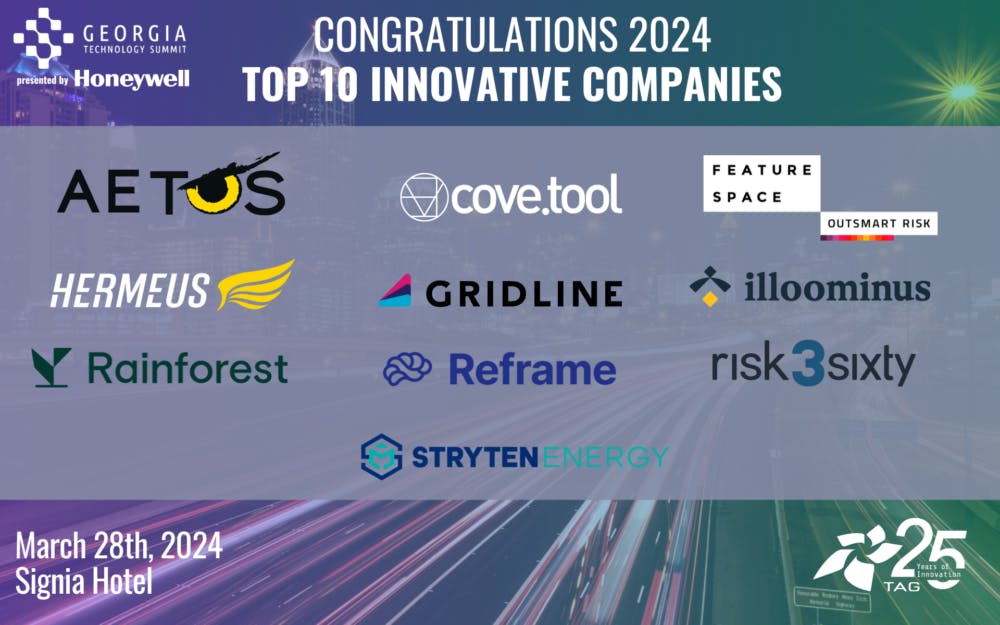
Aetos Announced As A 2024 Top 10 Innovative Company In Georgia
March 19, 2024
Continue reading ➔
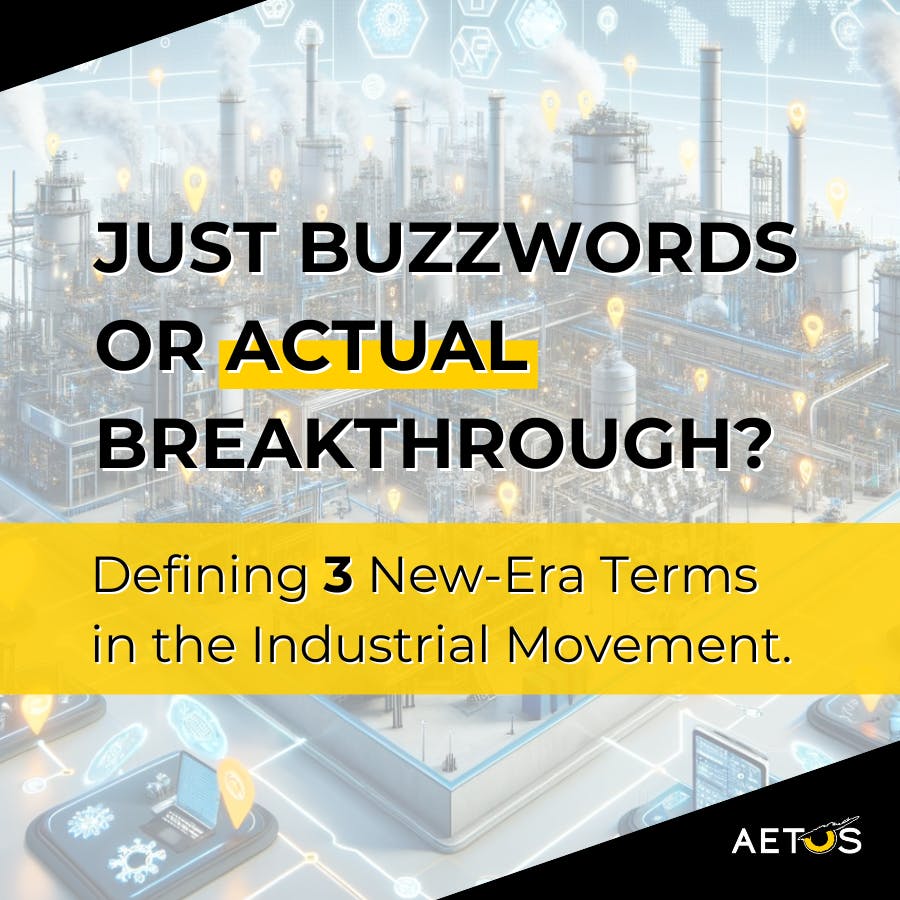
Just Buzzwords or Actual Breakthroughs? Defining 3 New-Era Terms in the Current Industrial Movement.
February 08, 2024
Continue reading ➔
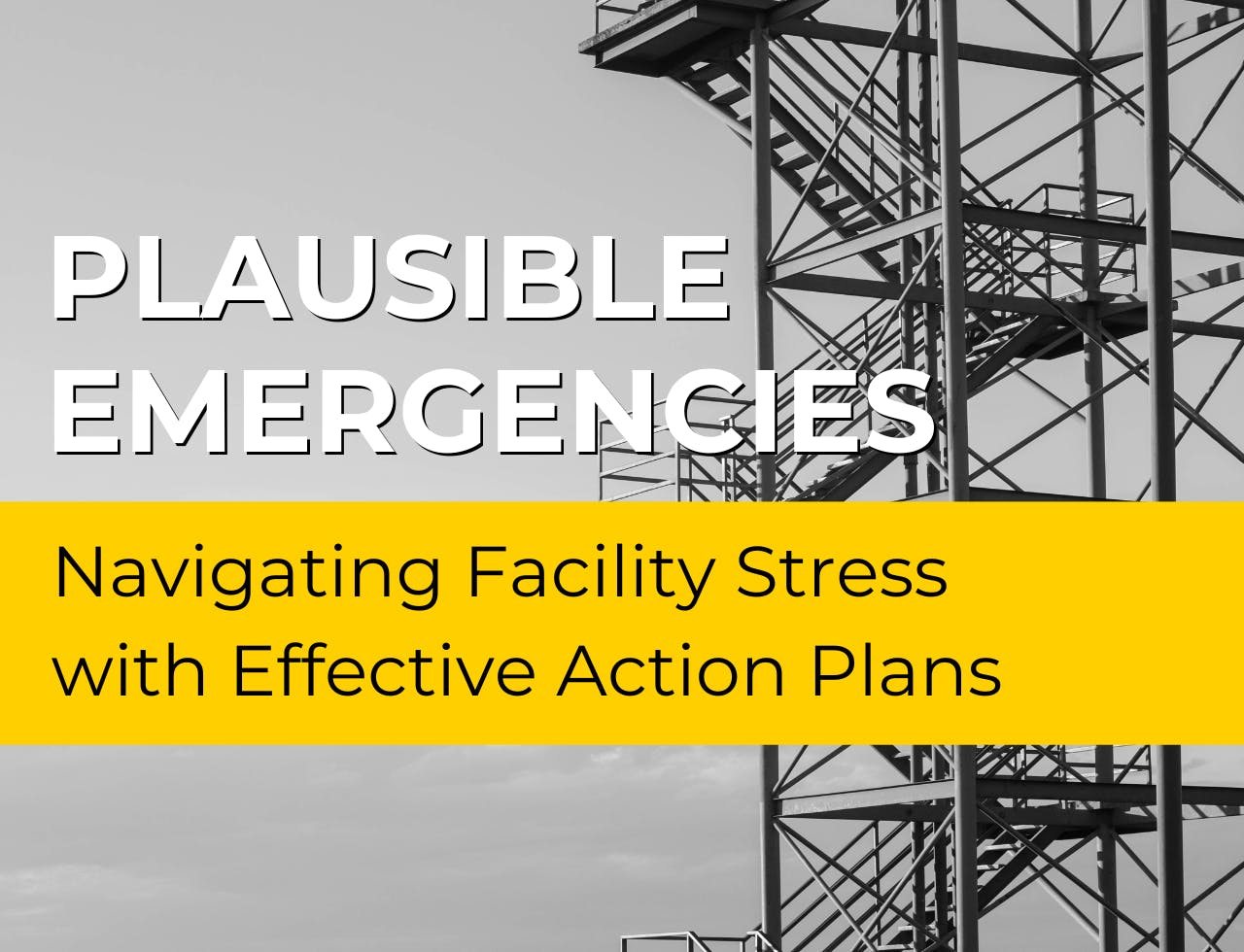
Plausible Emergencies: Navigating Building Stress with Effective Plans
January 10, 2024
Continue reading ➔
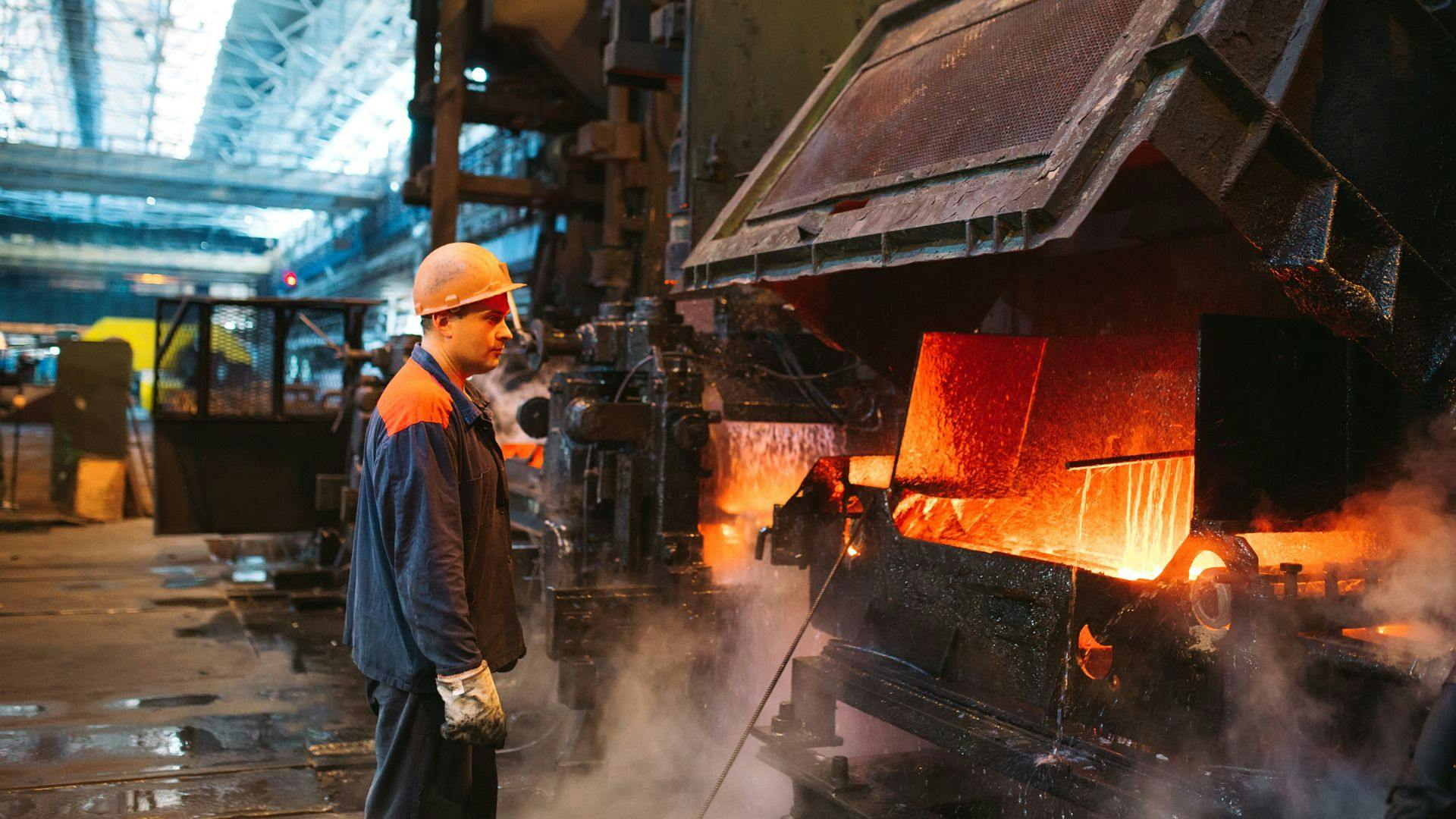
What is Continuous Improvement & How Should I Implement It?
November 30, 2023
Continue reading ➔
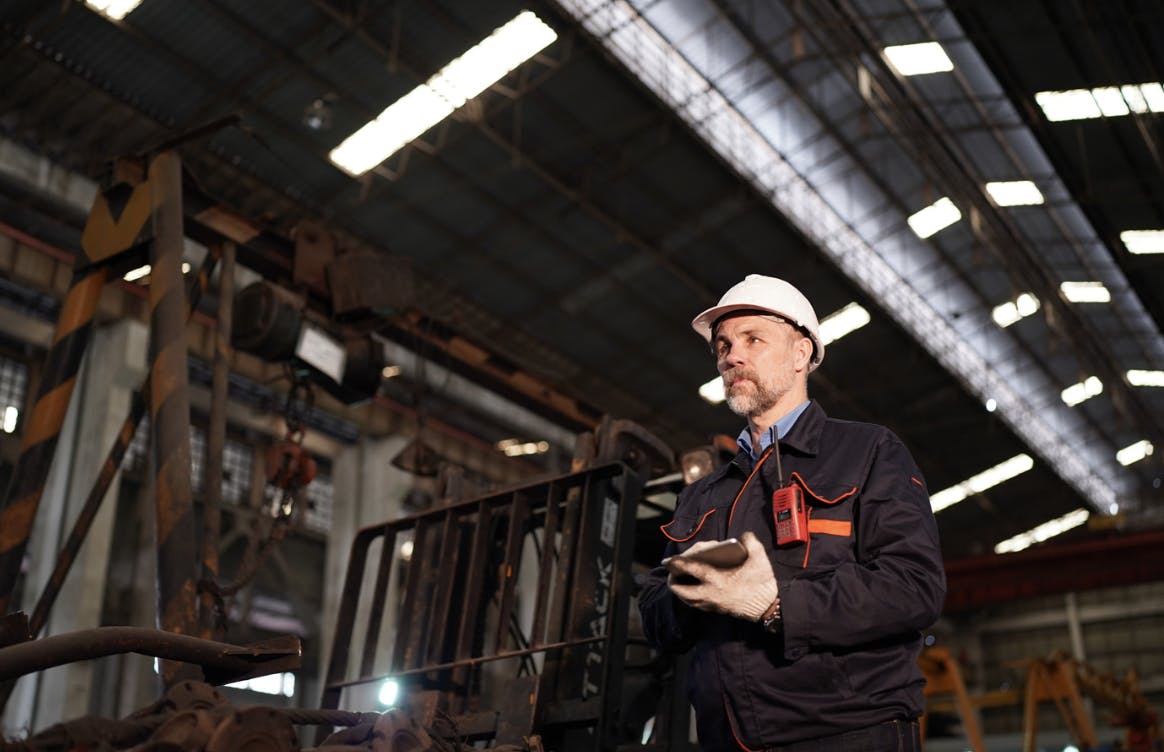
Efficient Knowledge Preservation: Aetos Operate for Institutional Knowledge
November 01, 2023
Continue reading ➔
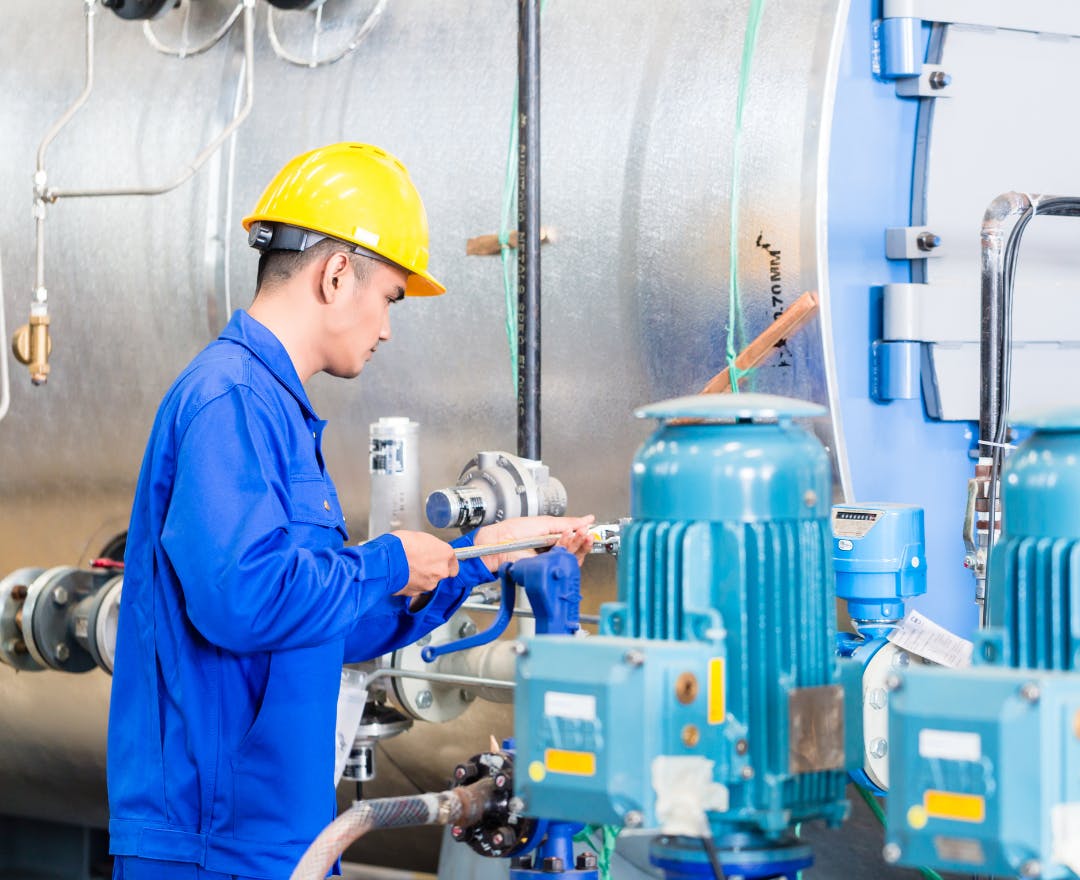
Accelerating Employee Onboarding: Aetos Operate in Action
October 18, 2023
Continue reading ➔
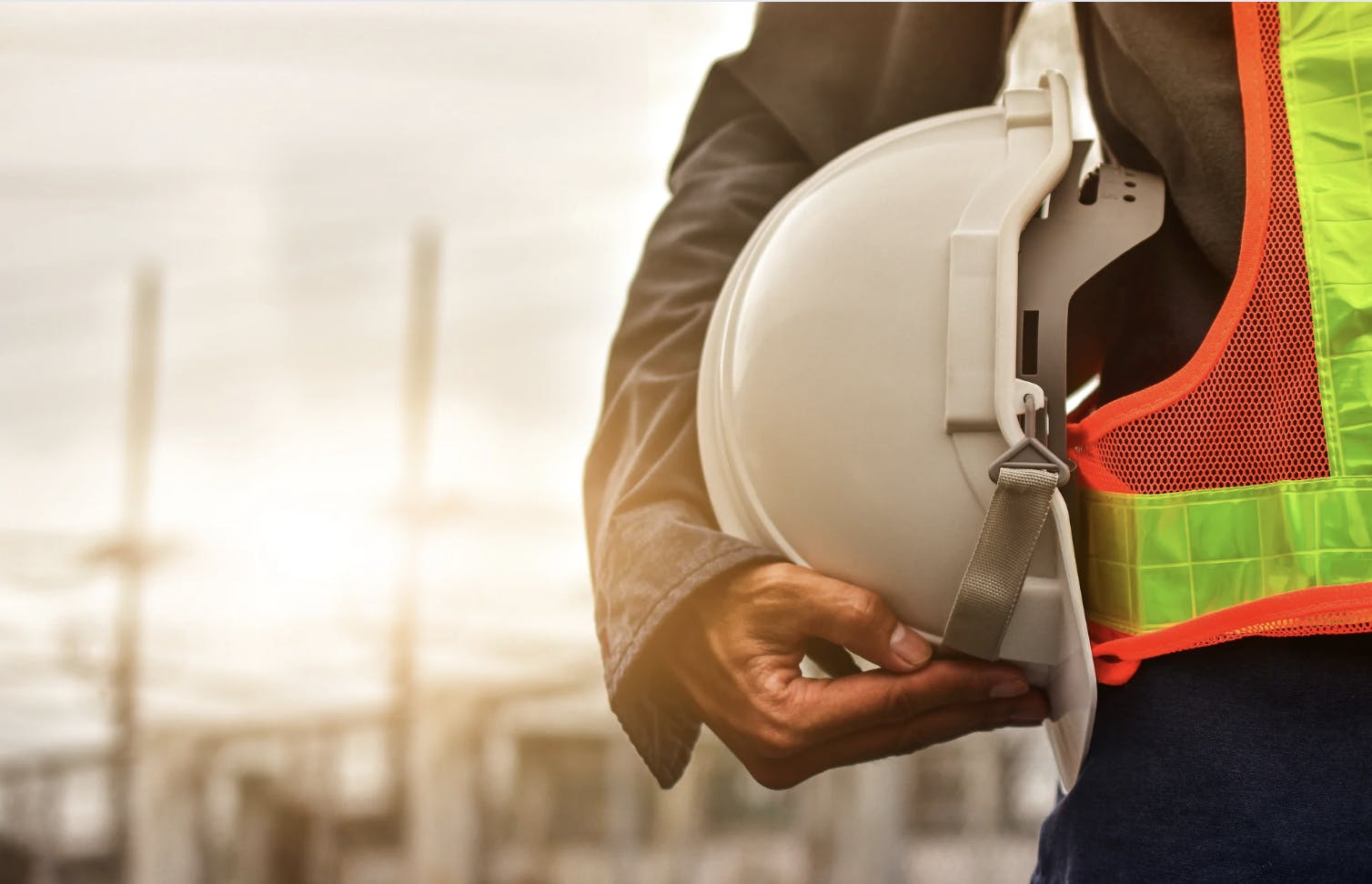
Is Your Team in Reactive Mode with Risk Management? Try Visualizing Your Facilities with Aetos
October 04, 2023
Continue reading ➔
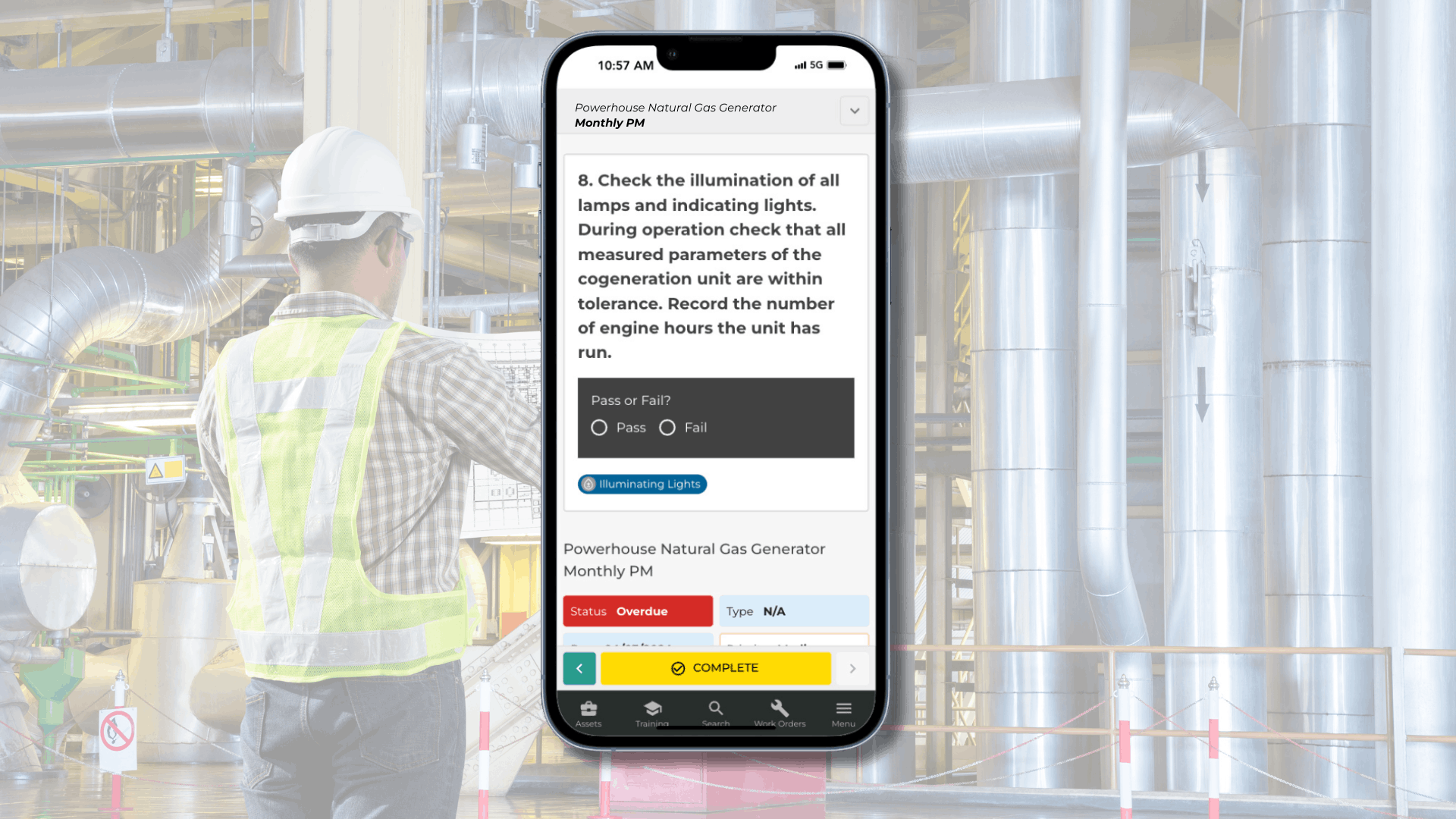
Embrace the Future of Maintenance with Aetos
September 13, 2023
Continue reading ➔
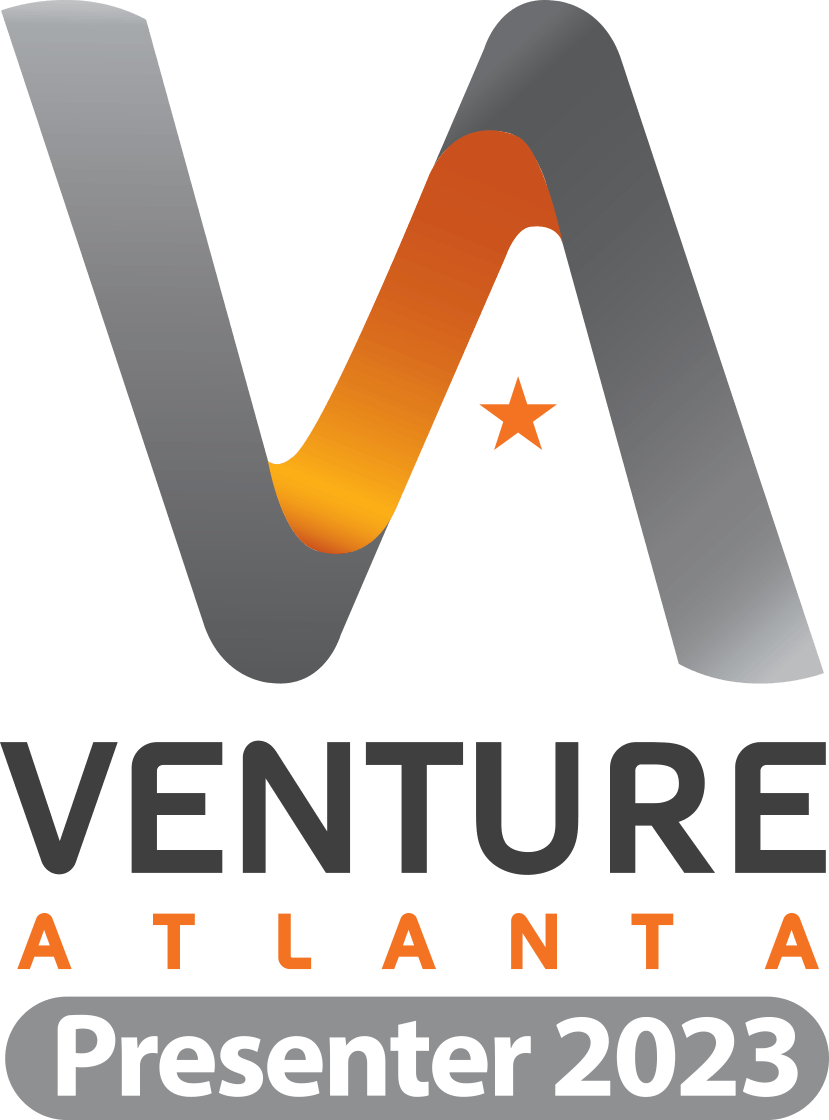
Aetos Imaging Selected as a Venture Atlanta 2023 Showcase Company
August 30, 2023
Continue reading ➔